Goodyear – Developing tyres for cars, sight unseen
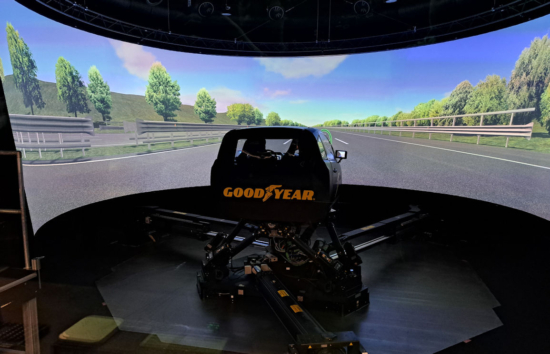
April 1 has been and gone this year, so there’s no danger in admitting that I’ve seen imaginary tyres being tested on cars that don’t even exist. No fooling. I’ve even driven with these non-tyres, at the Goodyear Simulation Center in Luxembourg. The illusion felt very real.
Resembling a premium arcade cabinet mated with a scaled down cinema, the Simulation Center is Goodyear’s answer to the challenges of developing original equipment tyres for today’s car parc. It offers a very effective means of keeping pace with vehicle development, saving time and resources into the bargain. More than a year after its commissioning, Goodyear inaugurated the Simulation Center on 26 March 2024.
Following this official opening, Tyres & Accessories visited the facility and sat down with Goodyear teammates who have close ties to the Simulation Center project. They explained the technology’s advantages as well as its current limitations and told us why tyre simulation has become an indispensable development tool.
“Our overarching goal at Goodyear is to enable mobility,” states Romain Hansen, who is the company’s vice president of product development for the EMEA region. “Around ten years ago we unveiled our ‘Beyond Tires’ concept, which focuses on developing various technologies, such as sensors and algorithms. The simulator in Luxembourg is part of this, how we will serve the mobility of the future.”
Changes we’re already observing and will continue to see include the growth of MaaS and fleet business within the consumer segment, a shift towards electric, connected and autonomous vehicles, as well as growing demand for sustainable products and processes. Each of these factors impacts upon how Goodyear develops products.
Cumbersome process
When delivering tyres for OEM customers, the traditional path taken by Goodyear (and other manufacturers) involves producing and testing physical tyres on prototype vehicles before taking lessons learned back to the drawing board. The exercise is usually repeated several times, leading Percy Lemaire to refer to this as a “cumbersome process.”
Elaborating, Goodyear’s senior director of tyre and science technology development comments that in today’s world, vehicles are growing in complexity and rely increasingly on software rather than hardware. “The possible combination of chassis set ups for various components is beyond the realm of physical testing. Therefore, virtual development has emerged as a natural way to deal with the performance of all those combinations.”
After working with finite element simulation for the past three decades, in 2020 Goodyear announced a significant investment in driving simulation technology. The initial step into this realm was compact simulators – units resembling a “sophisticated PlayStation,” as Lemaire puts it. The company then pushed the boat out with the purchase of dynamic simulation equipment for facilities in the USA and Europe. It turned to simulation solutions specialist VI-grade and selected the DiM250 driving simulator.
“Goodyear installed the first DiM250 in Akron, Ohio, as a suitable building to house it already existed there. At the same time, work began on a tailor-made premises in Luxembourg, about a kilometre away from the Goodyear tyre plant in Colmar Berg.” Including this new building, around 6 million euros went into the dynamic driving simulator in Luxembourg. The country’s government provided support for the project, and this is one reason why more than a year separated the centre’s commissioning and official opening – Goodyear decided to postpone the ceremony until after Luxembourg’s elections.
Replacing the car with data
What Goodyear gets for approximately 6 million euros is a facility that not only saves time and resources but also addresses a rapidly changing automotive landscape. One specific area of strength for the Goodyear Simulation Center is its suitability when developing original equipment tyres for entirely new electric vehicle models. The absence of predecessor models makes it extremely hard to conduct physical, real-world testing for these cars.
“We no longer need a car to exist to develop a tyre for it,” emphasises Laurent Colantonio, Goodyear’s senior director technology consumer EMEA. “Even without a physical car, the vehicle manufacturer can supply us with data for the chassis, suspension and steering system they are designing. They can tune and change this during the course of the car’s development and share the data with us.”
Simulation Center test drivers work with authentic sights, sounds and sensations (Photo: Stephen Goodchild / Tyre Industry Publications Ltd)
Virtual tyre models
Since commissioning the Goodyear Simulation Center in mid-2022, the team in Luxembourg has tested 122 tyre specifications. The first OEM partner to work with the DiM250 was Stellantis; the vehicle maker tasked Goodyear with delivering a bespoke version of its Eagle F1 Supersport for the second-generation Maserati GranTurismo in 265/30ZR20 (front axle) and 295/30ZR21 (rear).
“We exchanged tyre vehicle models with Maserati and were able to significantly reduce the number of iterations required to approve these complex tyres,” shares Colantonio. “We could converse with Maserati quickly whenever they adjusted the GranTurismo’s chassis, and we gained an edge from not having to pursue a moving target the entire time. We knew a major change to the car during development wouldn’t affect us like it would have with a physical prototype vehicle, which our tyre developers may have had access to for perhaps one week every quarter year.”
When working with physical prototype vehicles in its conventional original equipment tyre development programme, Goodyear typically produces up to six tyre iterations before gaining OEM customer approval. Testing in the Simulation Center has reduced this to an average of two iterations, and Laurent Colantonio says the team has even achieved a single full virtual iteration plus the final physical iteration when working with certain customers.
“Instead of submitting a physical prototype, we submit a virtual tyre model. The OEMs we work with have the capability to take that virtual model and assess, measure and judge it on their own capabilities, and provide us feedback to indicate whether we’re on the right track.”
Goodyear estimates that working with virtual tyre development and just one physical iteration for its entire current project portfolio would remove the need to produce 13,000 prototype tyres each year and avoid close to 100,000 kilometres of track testing. And instead of dispatching these tyres, along with the test drivers, to locations such as Applus+ IDIADA or the Nürburgring, the simulator can send them there at the press of a button in just two minutes.
The Simulation Center team can send a driver to another circuit, road or motorway at the push of a button (Photo: Stephen Goodchild / Tyre Industry Publications Ltd)
Tyre, road & vehicle
Locations can change in less time than it takes to brew a cup of coffee, but a trained driver requires several weeks of intensive training prior to testing with the simulator. Romain Hansen explains that with its nine degrees of freedom, a nine-metre screen and 270° field of view, the DiM250 simulator environment differs greatly from a physical track. “The motions are different, the visual information is different, and drivers need to get used to this. They need to acclimatise themselves with how all sights, sounds and sensations are fed back to the brain. Some people don’t feel very good after their first drive.” A few appetites may be ruined in the process, but about 90 per cent of Goodyear’s existing test drivers successfully transition to simulator testing.
The simulator brings together tyre, road and vehicle models. Percy Lemaire tells us that Goodyear’s focus is on the tyre models and how it can realistically bring these into the driving simulator. “We work with cross functional engineering teams to be able to make our tyre models as accurate as possible.”
The tyre model numerically represents the forces and movements the tyre is going to generate on the machine. The road model captures the friction between the road and tyre – Lemaire comments that there is “no such thing as just a road” as “every asphalt surface has different microstructures that are very important to the driving experience.” The vehicle model provides information about factors such as construction, damping, stiffnesses and rigidity and mass.
Although the DiM250 is an off the shelf unit, it offers Goodyear the opportunity to add its own knowledge. This means Goodyear can build years of learning, such as understanding the friction between tyre and road, into the simulation, giving its drivers an experience that competitors cannot necessarily replicate.
Bringing OEMs on board
The Goodyear Simulation Center complements the company’s physical testing but by no means replaces it entirely. Goodyear primarily uses the DiM250 to assess the dry handling and steering performance of its products and at present is working to extend the facility’s remit to ride comfort assessment. Wet and winter testing still takes place outside.
Should the need arise, the team in Luxembourg can collaborate with the Goodyear Simulation Center in Akron, USA. This facility also employs a DiM250 simulator, meaning that working together is just a matter of transmitting data. And when the day arrives that two simulators no longer suffice for Goodyear’s requirements, the mirrored design of the Luxembourg site lends itself to future expansion, with space already set aside for a second simulation unit.
“We have enough capacity for the years to come, but if we need to invest again, it will be within this building,” says Romain Hansen. A second simulator in Luxembourg would probably resemble the first, he adds, but have “different computing power behind it.”
In the meantime, Goodyear is inviting its OEM partners to make the jump from physical to virtual. Laurent Colantonio wishes to convince them that the Goodyear Simulation Center is not solely engaged in virtual tyre development, but rather in virtual vehicle development. “We cannot do it alone. We need to have the OEM on board, fully believing in it, agreeing to take a risk.”
Comments