Pirelli opens driving simulator at Virtual Development Centre
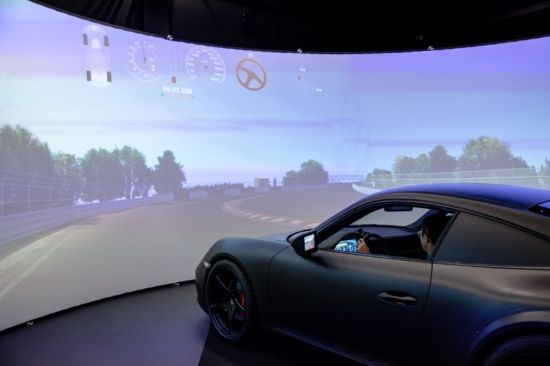
Pirelli has added a new driving simulator at its Virtual Development Centre (VDC) in Breuberg, Hesse. The latest generation of driving simulators have become an important tool for tyre manufacturers, reducing the number of physical prototype cycles required for the development of new products. Pirelli says the VDC and static driving simulator underline its innovation leadership, combining high-tech simulation, artificial intelligence, and expert engineering. Pirelli identified the VDC, which enables the premium tyre manufacturer to develop and test its products virtually, as a signifier of its commitment to investing in local production in Germany, contextualised by other premium tyre manufacturer’s recent announcements of the planned closure of tyre production facilities in the country. Pirelli’s Breuberg plant employs around 2,500 people, including 250 development engineers.
Pirelli says its latest investment in the plant offers considerable advantages for both Pirelli and its original equipment manufacturer customers. It says the digitalised processes result in a reduction of tyre development time by up to 30 per cent. The manufacturer also needs to produce up to 30 per cent fewer physical prototypes. As well as saving time and money, the company is also making a significant contribution to sustainable production.
Pirelli has set itself the goal of achieving CO2-neutral pro-duction by 2030. Furthermore, the driving simulator, as part of the virtual tyre development process, allows Pirelli to achieve increasingly precise results over traditional methods. It also aligns Pirelli with requests from car manufacturers.
“In our VDC, we can develop tyres for cars that don’t yet exist in reality, but which are provided to us by car manufacturers in the form of digital models,” explains Thomas Michel, chief technological officer at Pirelli Germany.
“Artificial intelligence (AI) and neural networks play an important role in this innovative tyre development. This is because they speed up the development of virtual tyre models enormously. What used to take hours or even days is now often completed in just a few seconds. It’s a sort of a virtual tyre factory.”
Pirelli engineers can enter virtual versions of all vehicle models provided by the car manufacturers into the simulator. Test drives then begin with the virtual tyre models. The engineers see how the vehicle behaviour is affected or should be affected by steering, acceleration, and braking interventions on the virtual vehicle.
“The VDC, including the simulator, supports all virtual project phases for German car manufacturers,” says Florian Waffenschmidt, head of VDC. “We virtually test tyres for combustion engines as well as our tyres with Elect technology for electric cars and plug-in hybrids.”
(Photo: Pirelli)
Comments