Continental – more than 120 years of retreading
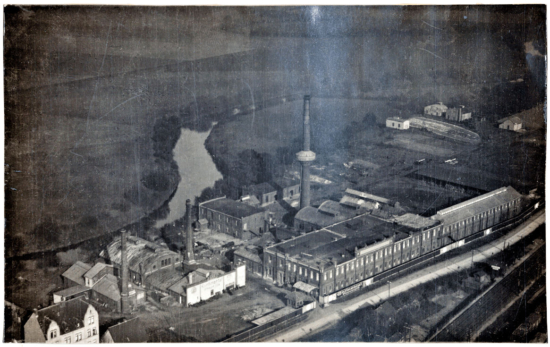
The word sustainability is in everybody’s mouths these days and retreading plays an important role here when it comes to tyres. But although fitting nicely with the zeitgeist, retreading has been around for quite some time. Continental, for instance, has been in the business for more than 120 years.
The origins of Continental’s tyre retreading activities can be found in its hometown of Hannover, Germany. The company began retreading tyres at is Hannover-Vahrenwald plant “more than 120 years ago” and in 1903 it acquired a factory building in nearby Seelze and set up a plant on the site for processing and recycling old rubber. The plant typically processed nine to 13 tonnes of used rubber daily.
Today, Continental retreads more than one million truck and bus tyres worldwide every year. According to a study by the Fraunhofer Institute for Environmental, Safety and Energy Technology (UMSICHT), retreaded tyres reduce CO2 emissions by up to 50 percent compared to new tyres. The amount of recycled and renewable materials in retreaded tyres can be up to 85 per cent. In terms of traction, grip and safety, Continental says its retreaded tyres are “every bit a match” for new tyres.
“We have been a pioneer in retreading truck and bus tyres for more than 120 years,” comments Jorge Almeida, head of Sustainability at Continental Tires. “Our tyre retreading saves raw materials and costs – a real win-win situation for fleet operators and the environment.”
The 70% club
Drawing information from industry reports and studies of tyre manufacturing practices, Continental estimates that as of 2022, 70 per cent of all truck and bus tyres are retreadable. Continental’s retreading activities include both hot/mould cure retreading in which the casing is restored from bead to bead in a hot vulcanisation process, a procedure the company calls ContiRe, or pre-cure/cold retreading, which involves applying a pre-vulcanised tread material to a buffed casing. Once again 70 per cent is the magic number, as Continental says both the mould cure and pre-cure procedures enable reuse of approximately that percentage of the original tyre. Retreading also requires up to 70 per cent less energy compared to the production of a new tyre.
Since 2013, the Hannover-Stöcken plant has retreaded around 900,000 truck and bus tyres (Photo: Continental)
More than 120 years after retreading its first tyre, Continental still retreads in Hannover. It established a new ContiLifeCycle facility, combining a retreading and recycling plant, in the suburb of Stöcken in 2013. With an integrated approach consisting of mould cure retreading for truck and bus tyres as well as a rubber recycling system developed specifically for the ContiLifeCycle plant, the company has been actively promoting the sustainable use of raw materials, water and energy for a decade. Since 2013, the Hannover-Stöcken plant has given around 900,000 truck and bus tyres an extended service life through retreading.
Comments