Fraunhofer Institute research shows pyrolysis benefits
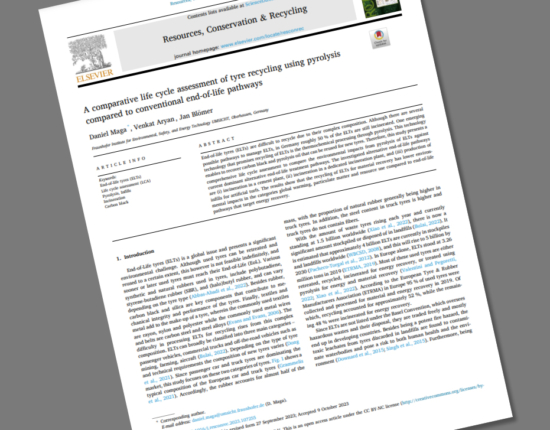
Currently around 4 billion waste tyres reside in stockpiles and landfill around the world, a number that is projected to reach 5 billion by 2030. In Europe alone, ELTs stood at 3.26 million tonnes in 2019, and while 95 per cent of these were collected and processed, around half were incinerated for energy recovery.
A scientific study conducted by researchers from the Fraunhofer Institute highlights the significant CO2 savings that the pyrolysis process offers compared to such methods of tyre recycling. The paper by Daniel Maga, Venkat Aryan, Jan Blömer, titled ‘A comparative life cycle assessment of tyre recycling using pyrolysis compared to conventional end-of-life pathways’ and published in the journal Resources, Conservation and Recycling (Volume 199, December 2023) contrasts Pyrum Innovations’ pyrolysis process against three other methods for disposing of end-of-life tyres (ELTs) – their processing as refuse-derived fuel in cement kilns and as fuel in dedicated power plants, as well as the treatment for material recycling, to make infill products such as artificial turf and rubber mulch.
ELTs pose significant environmental and health risks when discarded in landfills, releasing toxic leachates and taking centuries to degrade. Controlled incineration, while offering energy recovery, requires high temperatures and expensive equipment to mitigate pollutants. The energy recovered from incineration only constitutes a fraction of that required to produce new tyres.
While various recycling methods exist, the complexity of ELT composition, including crosslinked structures and impurities, limits closed-loop recycling. Current practices mainly result in downcycling, with ELTs finding use in applications like road construction, railway sleepers, and artificial turf infills.
LCA comparison
Thermochemical processing via pyrolysis offers promise in recycling ELTs, recovering carbon black and pyrolysis oil for reuse in new tyre production. Maga, Aryan and Blömer use a comprehensive life cycle assessment (LCA) to examine the environmental impacts of pyrolysis against dominant alternative treatment pathways such as incineration in different settings and producing infills for artificial turfs. The paper applied LCA methodology to investigate the environmental impacts generated from all four end of life handling and processing pathways for ELTs, using one tonne of ELTs as a functional unit.
The LCA methodology they employed adheres to ISO standards and focuses on comparing the environmental impacts of different ELT handling and processing methods. The study evaluates Pyrum Innovations’ pyrolysis technology, emphasising its multi-stage process for recovering valuable substances and energy from ELTs.
The Pyrum process
The patented Pyrum Innovations pyrolysis technology is a multi-stage, energy self-sufficient, and continuously operating system. It is designed for the fractionated recovery of raw materials and energy from pourable, cross-linked organic compounds of high molecular weights, specifically focusing on granules derived from ELTs. During operation, granules from ELTs gravimetrically pass through a vertical, multi-stage pyrolysis reactor from the top to the bottom, wherein said granulates are pyrolysed at temperatures between 500 and 700ºC. A subsequent two staged fractionated condensation of the pyrolysis vapours allows the recovery of oil and gas compounds, and the use of pyrolysis gas in a combined heat and power plant (CHP) provides the electric power required for heating the pyrolysis unit.
In the research published in Resources, Conservation and Recycling, Maga, Aryan and Blömer utilise data from Line 1 at the Pyrum plant in Dillingen, Germany.
Material recycling the preferable option
What Maga, Aryan and Blömer found is that the material recycling of ELTs by pyrolysis or production of infill offer lower environmental impacts in regard to global warming, particulate matter and resource use compared to energy recovery in cement or incineration plants. The recovery of carbon black via pyrolysis shows similar benefits as the production of infill, but the study did not consider an additional advantage of pyrolysis, namely that this method can also be used to recycle infill.
Pyrum Innovations sees it process as a clear winner: “The results show that the recycling of old tyres through Pyrum pyrolysis is significantly more environmentally friendly than other methods in the categories of global warming, fine dust and resource consumption. Overall, the Pyrum pyrolysis process results in a CO 2 saving of 703 kg CO 2 equivalent per ton of used tyres.” For comparison, Pyroum notes that the current recycling mix in Germany achieves a saving of 561 kg CO 2 -eq. per tonne of ELTs.
“The pyrolysis of used tyres using the Pyrum process is superior to conventional recycling methods,” states Pascal Klein, chief executive officer of Pyrum Innovations AG. “In addition to the LCA carried out by Fraunhofer UMSICHT last year, the study results now published include real operating data from the mill and the agglomeration. This makes the database very reliable and the results underline the enormous potential of Pyrum pyrolysis technology in used tyre recycling.”
Appropriate ELT management vital
In conclusion, the article stresses the importance of proper ELT management to prevent environmental hazards and the accumulation of waste. Material recycling emerges as the preferable option over energy recovery, although recycled products may pose risks such as plastic emissions and leaching hazardous substances. Regulatory discussions about restricting certain applications for recycled ELT products underscore the significance of technologies such as thermochemical processing in effectively managing and valorising ELTs.
Comments