Leading the way in commercial tyre retreading innovation: ContiLifeCycle UK plant
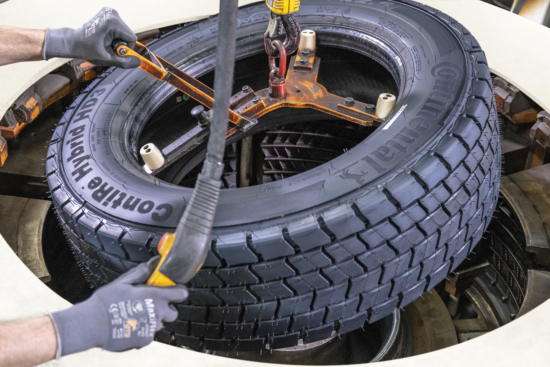
Continental demonstrates investment and automation at rebranded Bandvulc plant – a key pillar of its European sustainability strategy
Tony Mailling, plant manager of the ContiLifeCycle plants in Ivybridge and Stöcken (Photo: Continental)
Continental relaunched the Bandvulc retreading plant it acquired in 2016 as the ContiLifeCycle plant in March. Based on what Conti EMEA’s head of commercial consumer solutions Ralf Benack described as the existing “deep knowledge” of Bandvulc, the facility in Ivybridge, Devon has become a technical innovation hub for the company’s tyre retreading programme in the region. When Tyres & Accessories visited the plant later in the year, the manufacturer revealed the results of strong annual investments and its innovative implementation of automated processes for increased efficiency, and the key role that reatreading plays in Conti’s overall sustainability strategy.
The influence of the Ivybridge plant within Continental is also strong, as it often provides a developmental blueprint for the ContiLifeCycle plant in Hannover-Stöcken, near Conti’s headquarters. The links between the facilities are strong. Plant manager Tony Mailling now serves a dual role as the Stöcken plant manager under his remit as head of hot retread production EMEA, while buffed material from Ivybridge is shipped back to Stöcken for use in compound production.
The symbiosis between the two plants promotes further development in the retreading manufacturing processes that, according to Benack, are helping to back up the position that a “retread tyre is as good as a new tyre”. Manufacturing processes are increasingly similar to new tyre building, with the input of used casings replacing most of the construction phase. Through the implementation of such features as conveyorized transport throughout the production line, robotic casing skiving, the application of water-based, automated adhesive spray, and automated tyre building machinery, Continental has harnessed production expertise to ensure its Bandvulc and ContiRe branded retreads are able to support the same performance guarantees it offers it offers to fleets running its new tyres.
Ivybridge history and innovation
Casings at the ContiLifeCycle plant (Photo: Continental)
The depth of the knowledge base in Ivybridges extends back to the 1970s, Mailling told T&A. Founded to serve commercial vehicles employed in the construction of the Exeter-Plymouth trunk road, an extremely large regional infrastructure project connecting the north and south coasts of Devon, Ivybridge added compound mixing in the 1980s, and developed into a leading retread tyre supplier to the waste and recycling industry in the 1990s, introducing innovative kerbing protection into retreads, which were a natural choice for operation in environments where tyre damage is inevitable. As we have seen, the innovation has continued – and even accelerated – into the 2020s, following the plant’s merger into Continental in the mid-2010s. The development of people-less warehousing has joined the conveyor system connecting the plant’s three buildings to vastly improve the plant’s ergonomics, minimising manual handling. As a result, Ivybridge and Stöcken lead Conti’s manufacturing footprint in terms of safety, Mailling says.
Future innovations are also continuing to support the ContiLifeCycle plant’s product quality and operational sustainability. Mailling says Ivybridge will expand robotic skiving capacity with the introduction of a second machine, while more automated buffing will target greater efficiencies in sidewall and tread removal. Conti wants to remove the final piece of manual handling at the plant by introducing automated press-loading. It is also working on improvements to its tyre building processes with the expansion of fifth generation Continental commercial tyre production, which will target lower rolling resistance.
“The key role for Ivybridge celebrates the skill, expertise and effort that the team has invested into transforming the image of retread tyres,” Mailling says. “Where once there were misguided doubts about the quality of retreads, today the science, technology and engineering know-how involved in the retreading process makes it easily one of the most advanced areas of tyre production.”
The plant is also working on furthering the sustainability agenda with a raft of energy-saving and resource-saving measures. It is installing rooftop solar panels to generate renewable energy for use on-site, for example. Meanwhile the material removed – around 7kg of rubber dust from casings accepted into retreading production and 34kg from scrapped casings – is recycled. The plant operates on a 0% to landfill waste management policy too.
Casing policy
The automated pick and place system in the casing selection hall (Photo: Continental)
The ContiLifeCycle plant casing strategy is notable, given the commitment to maximising resources. Ivybridge is pragmatic about its collection operation, collecting used commercial tyres from all brands and warehoused in Wigan, Rugby and Ivybridge, where finished products are also stored. The benefit of this is a relatively reliable casing input level, which offers a competitive advantage since supply is not throttled by particular brands’ new tyre sales, totalling around 500,000 per annum. Around 30 per cent of this total is scrapped – responsibly, as previously mentioned – while a further 10 per cent is deemed unsuitable and sold on. The plant’s own fleet of 22 trailers is operated efficiently with circularity; more tyres come in than go out due to the rejection of unsuitable casings, but this is balanced by scrap removal.
To process this level of input, casing inspection operations run 24-hours per day, five days a week, like the three-shift cycle of the rest of the plant. Suitable casings can be made into new retreads on the day of arrival, but the plant stocks 18-20,000 casings at any time. 10,000 casings are processed weekly, with up to 4,000 retreads produced. In the inspection hall, two shearography machines check for voids and separations in the casing structure, while robotic warehousing is used to stack and select casings as required. A barcoding system allows Conti to track tyres through factory processes and beyond, as the tyre’s barcode is engraved on the sidewall and its data captured for future reference.
Overall, retread production is largely split between Bandvulc branded tyres, which utilise a wide variety of casings, and ContiRe, which use Continental casings.
- The rebranded ContiLifeCycle plant has invested in innovative automation and robotics solutions, such as the automated skiving machine (Photo: Continental)
- Tyre building ready for hot cure retreading (Photo: Continental)
- Inspecting the casings (Photo: Continental)
- Rejected casings bailed ready for recycling (Photo: Continental)
- Buffed rubber (Photo: Continental)
- Final inspection of the new retread tyre (Photo: Continental)
Automated buffing and building
Bandvulc Wastemaster 5 (Photo: Continental)
Once the casing is selected, it is conveyed into the buffing area where five automated TRM5 buffing machines, named after the Knights of the Round Table, complete the buffing process. The robotic skiving unit, which is due to be joined by a second such machine, was developed jointly with a local robotics firm. It has a throughput of 8-10 tyres per hour, detecting and removing casing injuries and implementing rubber-only repairs to the first belt. Mailling tells T&A this results in operators working 30 per cent quicker. Around 10 per cent of casings that make it to this point are also rejected for retreading due to injuries too severe to mend acceptably.
After this is the facility’s second generation pick and place warehousing system, which was implemented after engineering improvements made by Ivybridge staff. This is the unit that has been replicated and installed in Stöcken, having increased space efficiency with a raised track for the transport arm.
After selection, casings are then transported through adhesive spraying and into the building and curing processes. Two Marangoni building machines have been optimised and automated to make a third obsolete, while 54 presses allow for a high volume of product variations produced by the plant – eight new CIMA presses are used specifically for ContiRe production. After a final visual inspection, the final retreads are transported by conveyor back into the warehousing hall in readiness to be loaded onto trucks, completing a circuit of the plant.
The level of automation raises an obvious question about staffing levels at the plant. Mailling notes the automation is allowing the plants 85 staff working across a three-shift pattern on the shop floor to develop more skills, both in maintaining and operating machinery and extending this technical knowledge to upskill.
Ralf Benack (Photo: Continental)
Conti’s overall investment in the plant since it was brought into the group has averaged around £1.5 million per year, with a similar level of sustained investment put into the newer Stöcken facility. Both plants are developing under five-year plans in the ways demonstrated during T&A’s visit: increased automation and a focus on sustainability in manufacturing, recycling, and the production of higher quality retread tyre products, such as fifth generation versions of popular product lines like the Bandvulc WasteMaster and CityMaster, and the premium ContiRe brand retreads. Of the latter, Conti believes the EcoPlus HT3+ is a “tyre of the future” – an example of the direction in which the manufacturer wants to take retreads. It combines “good as new” looks with “another level” of rolling resistance optimisation in the Euro VII trailer tyre market.
Conti is using the facility as a “promotional tool” for fleet customers too, improving the perception of retreads along the way, and demonstrating how they can be used as part of a fleet tyre strategy alongside new tyres, fleet management technology, and the Conti360° service network to achieve the Holy Grail, which Benack identifies as “Lowest Overall Driving Cost”.
Comments