Skim extra profit with brake lathes
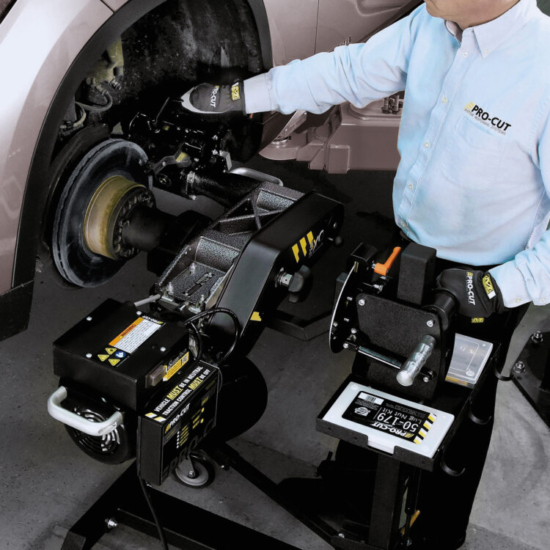
Our delayed but still planned departure from fossil fuels will transform the automotive landscape, but how vehicles stop will likely remain fundamentally unchanged. Tecalemit thus points out that brakes may be one of the few components that garages can still service. That being the case, the garage equipment supplier emphasises it is “essential that workshops up their game in what has perhaps become an overlooked source of income.”
The answer, says Tecalemit, is to have the “right skills and equipment” – and for garages, this may well be an on-car brake lathe. Although Tecalemit concedes that brake disc skimming may be viewed as an “old-fashioned practice” in an era when replacement is the rule and repair the exception, this is a job that often makes sense.
Take brake judder. One of the most common causes of this is disc thickness variation (DTV). To brake effectively, the disc needs to have the same thickness throughout, otherwise intermittent contact between the pad and disk will result in a judder felt through the pedal or steering wheel. DTV can easily be fixed by skimming discs, but most brake disc manufacturers’ suggested remedy is to replace the discs and pad. And while many garages recycle scrap metal, this is an incredibly wasteful way to solve a simple problem.
Disc skimming can also prevent issues from occurring. Generally, brake discs last up to three times longer than pads, and Tecalemit considers pad replacement an “ideal time” for a workshop to skim the discs. “Like rebalancing a wheel after a tyre change, skimming the discs when changing the pads improves performance and reduces the chances of complaints. And as a bonus, it can increase the revenue earned from the job.”
A new source of income
Tecalemit notes that the question of how much extra revenue a workshop can generate is very subjective. There are many variables to consider, including labour rates, competitors and how much a customer is willing to pay. “However, the time it takes to skim the discs on an axle is around 30 minutes and given an average labour rate of £80 per hour, a charge of £40 per axle should be very realistic. Considering that a Pro-Cut X9 on-car brake lathe typically costs just over £40 per week to lease (over 60 months), it’s easy to see how it can start paying for itself.”
Skimming discs isn’t just better for the environment, says Tecalemit; it’s better for the driver and the workshop’s bottom line. The garage equipment supplier adds that a Pro-Cut on-car brake lathe doesn’t just offer a solution for some of the most common causes of brake issues, it also provides a way to enhance the service a garage offers and generate extra income. “So, whether a workshop is looking to reduce the amount of waste they produce or for a way to add value to the service they offer, a Pro-Cut brake lathe can be a worthwhile investment.”
Comments