Wastefront granted Environment Agency permit for Sunderland site
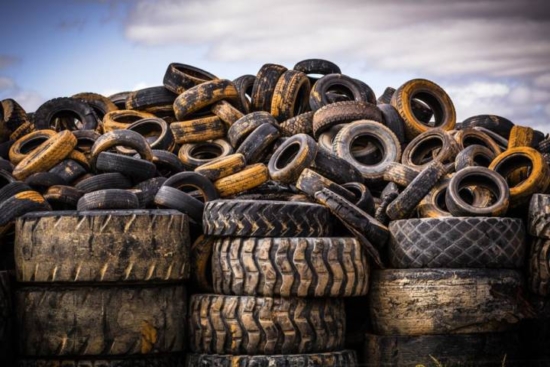
At the end of August, Wastefront was granted an environmental permit for its Port of Sunderland site. The decision clears the way for the next stage in the process, with Wastefront working toward having the site fully operational by 2026.
The Environment Agency report explaining its decision to grant the environment permit reveals details about Wastefront project. First, the application and approval is based on a site capacity of 77,000 tonnes of end-of-life tyres per year. Next, Waste tyres will be delivered as bales of whole tyres which will be stored in external bays, with a maximum pile size of 300m3.
The tyre storage building is roofed and enclosed on three sides. The overall stockpile volume has been sized to provide 3-5 days processing capacity and to align with the requirements of guidance on Fire Prevention Plans (FPPs).
From the main tyre storage area, bales will be transferred to interim storage adjacent to the shredding process building by forklift truck into two stockpiles. The maximum size of any stockpile in this area will be no greater than 300m3.
Tyres will then be shredded with the removal of steel wire using magnetic separators. Approximately 50 kg/h of dust, predominantly comprising fabric and rubber, will be produced between the two lines which will then be collected in drums and stored in the main bale storage area pending transfer off-site for treatment or disposal at an appropriately regulated facility.
Project to feature three pyrolysis lines
Wastefront Sunderland will feature three pyrolysis lines located in an enclosed building, each consisting of four reactors, designed to operate at a capacity of 20,000 tonnes per year of tyre chips on a continuous basis. The reactors break down the tyre chips into a hydrocarbon vapour and a solid char which comprises carbon black, amorphous carbon, inorganic fillers and residual steel.
The pyrolysis reactor will be heated by “an external jacket through which a combination of exhaust gas from the burning of fuel gas (produced by burning the process gas from the gas holder and distillation stage) and hot recycled exhaust gases from the heat recovery fan is fed.” During start-up, the fuel gas can be supplemented by natural gas, however in normal steady operation there will be a slight surplus of fuel gas.
Each reactor features a water-cooled screw conveyor sealed with the reactor, which removes and cools char from the pyrolyser. As the process continues, the char is then transferred into a water-cooled elevator for further cooling before the solids are deposited on to an output conveyor for further processing in the recovered Carbon Black (rCB) area.
Fine steel is removed at this point, collected and baled for recycling off-site. Solid residue (char) is milled, pellitised and dried to produce carbon black.
The pellets proceed to a fluidised bed dryer, which is fed with air heated from the combustion of pyrolyser gas in a fired heater. Air leaving the dryer passes through a filter unit to remove fines, which are collected in drums before being recirculated back through the pellitisation process and is then fed to the regenerative thermal oxidiser to ensure any trace hydrocarbons, carbon monoxide or other contaminants are destroyed.
Commenting on the news, Wastefront CEO Vianney Vales said:
“Wastefront’s work is timely and urgent; our Blueprint will solve the disposal of an estimated 31 million metric tonnes of End-of-Life-Tyres annually, which is currently a concerningly dense source of both emissions and waste. Our Blueprint will reduce emissions and bring circularity to heavy industry, at a scale not seen before.
“We are therefore delighted to have been granted an environmental permit for our Sunderland site – it’s a vital step on the journey to having the site fully operational by 2026. The entire team can now focus on starting construction and investing further in Sunderland…”
Matthew Hunt, Director at Port of Sunderland, added:
“We are delighted that Wastefront has received an environmental permit for its world-first tyre recycling plant here at Port of Sunderland.
“Representing an investment of over £100 million, once completed, the facility will represent a critical piece of UK infrastructure, creating highly skilled jobs for local people at the Port and significantly consolidating further our position as an investment location of choice for the ever-growing circular economy.”
The complete environmental permit report can be read here:
Comments