30 million retreads and counting: Michelin celebrates 100 years of tyre re-manufacturing
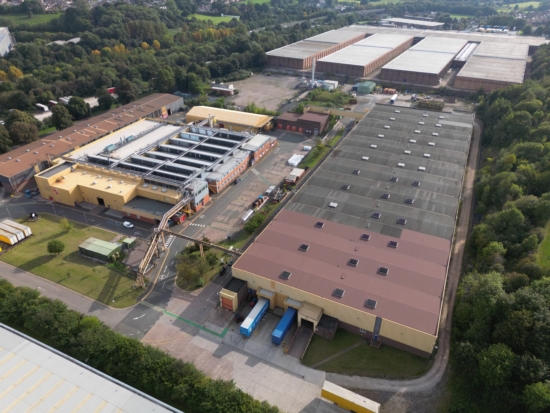
Michelin started retreading tyres back in 1923. In the years that followed, the process was refined and demand grew, with the Michelin Remix process (REmould, MIchelin, and X the designation for the French tyremaker’s radials) born in the 1960s. Demand for retreads continued to increase, leading to the expansion of production at the Stoke-on-Trent plant in 1968. Since then, around 30 million worn tyres have been remanufactured at the Michelin plants in Stoke-on-Trent, UK and Homburg, Germany. With around 10 million of those retreads manufactured at the Campbell Road, Stoke-on-Trent operation, Tyres & Accessories went to see the latest developments at the largest retreading facility in the UK and arguably one the most modern retreading facilities in Europe.
Stoke-on-Trent has been home to Michelin in the UK since 1927, with a retreading facility on site since 1968.
Around 60 per cent (and as much as 75 per cent) of retreads produced in Stoke-on-Trent are destined for fleets operating in the UK and Republic of Ireland, with the remainder exported to mainland Europe.
In Stoke-on-Trent, the retread factory operates with a workforce of 180 people, spread across three shifts per day, five days per week, 24 hours a day. The team is highly skilled and qualified, with some factory roles requiring up to six months on-the-job training.
Michelin’s Campbell Road Remix facility combines the latest bespoke technology, with the experience of skilled operators (Photo: Michelin)
As Vincent Gridel, Factory Manager, explained: “You don’t achieve the consistent levels of quality we deliver with our Michelin Remix and Encore product without an extraordinary effort. Yes, we rely on some highly complex and often bespoke machinery as part of the retreading operation – but we also need a team which knows the process intricately and can maintain our high standards with every single retread tyre they produce.
“We have people in the factory who’ve been doing the job for decades, some since they first joined Michelin as an apprentice. Plus, we have colleagues whose parents and grandparents have worked here before them. Michelin has been synonymous with Stoke for generations, and we’ve built up a fantastic loyalty and skills base which we believe is unmatched in our industry.”
Michelin estimates that the European tyre retreading sector is responsible for around 32,000 skilled jobs, often concentrated in industrial areas which are reliant on the tyre industry for employment opportunities.
Gridel adds: “Compared with the importation of non retreadable single-life truck and bus tyres, we generate a number of job opportunities. It’s not something that’s often considered, but a fleet retreading its tyres with us is supporting UK manufacturing, UK employment, and doing their bit for the planet.”
Encore, encore
Also housed within Michelin’s retread facility in Stoke is the Encore operation, which follows a similar process to Remix, but offers the potential to extract additional lives from a worn Michelin Remix casing as well as the chance to reuse tyre casings originating from “a selection” of other manufacturers.
One of the key benefits of Encore is that it allows an operator to undertake a smooth switch over to a Michelin policy from a competitor tyre brand. This is achieved by taking old tyres which pass Michelin’s quality standards and processing them as Encore, whilst at the same time introducing Michelin new and Remix tyres onto the vehicles.
Michelin is very open about the origin of its Encore tyres. Sidewall markings reveal whether it has been manufactured from a Michelin Remix casing (a Grade M), one of several other major brands (Grade 2), or a good condition casing sourced from another but still reputable manufacturer (Grade 3).
Michelin UK and Ireland B2B sales director Andrew French explained: “The Encore range is central to our circular economy solution, reducing raw material usage and ensuring we extract the maximum performance out of every possible tyre casing. The fact we can even retread a worn Remix casing for an additional life in service is testament to the quality of our verification and manufacturing processes in Stoke-on-Trent.”
For complete coverage of T&A’s visit to Michelin’s Campbell Road retreading facilities, including an account of the Remix production process and details of the latest factory updates, see October’s edition of the magazine.
Comments