Artisanship alive & well in tyre development
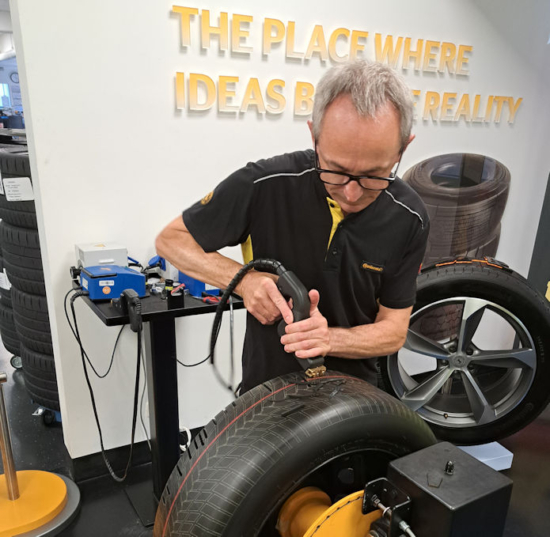
During the final year of primary school, my friend Brad decided to immortalise himself with a penknife, a wooden bus stop bench serving as his canvas. Two memories remain of that afternoon. First, by misspelling his own name Brad ensured he’d be known as ‘Bardles’ for the remainder of his school days. I also learned that engraving was nowhere near as easy as it looked and required a very steady hand.
The second of these lessons returned to me many years later as I watched a perfect tread pattern emerging on a previously smooth and featureless tyre. I never realised that the modern tyre development process left room for such artisanal skill, but even the biggest in the business still rely upon the talents of qualified tyre carvers.
“When it comes to tyre carving, the first thought is that it’s old fashioned, that things aren’t done this way today,” comments Wolfgang Recker, who is head of Tire Carving & Mechanical Processing at the Continental facility in Hannover-Stöcken, Germany. Together with a colleague who he introduced as Martin, Recker dispels this assumption and demonstrates why tyre makers such as Continental still rely on good eyesight and steady hands.
What we quickly discover is that when working with small batches of tyres or making modifications to existing tread patterns, automation doesn’t necessarily offer a time advantage, and carving is much less costly than working with a tyre mould.
Accuracy & patience a must
The carving process begins with the receipt of a new tread design. Wolfgang Recker explains that once the development engineer or designer has sent this, the tyre carving team’s first task is to copy the tread onto a transparent plastic foil. This pattern is then painted onto a vulcanised but smooth tyre with a tiny drill. “We have to do this very accurately, the error tolerance is no more than ±0.2 millimetres,” notes Recker. Once they’ve drawn the tread pattern upon the tyre, the carvers unpack their knives. And these are no ordinary knives.
“We designed the knives ourselves,” elaborates Recker. “Each has a light at the front and can be adjusted to different angles, width or depth. It is also movable at the front.”
Carvers typically need 20 to 40 hours to cover a smooth tyre with a new summer tread. Extensive siping increases the time to 40 to 80 hours when carving a winter tread, but the finished products are indistinguishable from tyres fresh from the factory. Recker confirms that “every tyre we carve here can be tested in the same way that a production tyre is tested.”
In addition to producing prototype tyres, Continental’s carvers make custom tyres for display purposes (Photo: Tyrepress / Stephen Goodchild)
Robotic rivals
Yet there’s a significant difference between the carved and production tyres. The mould that the production tyre comes out of costs between £25,000 and £70,000 and takes months to arrive after being ordered. “This is the reason why we carve tyres. We are more efficient and quicker,” comments Recker. This leaves the tyre carver with but one rival – automation.
Continental has employed robotics for prototype tyre development since 2014, with units such as the Stäubli RX160 six-axis robot operating within the Hannover-Stöcken facility. Robots aren’t union members and rarely take sick leave (although Recker observes that when automated carving equipment gets ill it is “very expensive”), and they don’t need the frequent breaks that are essential for carvers to relax their eyes and neck muscles. But automation isn’t just speed and convenience without any drawbacks.
Recker points out that when his team “receive drawings of a tyre tread, “we have to translate this pattern into the robot’s language. This takes a lot of time. We must determine if it makes sense to produce the tread by hand or whether to program the robot.”
The decision is an easy one when tweaking existing patterns. For example, if a tyre engineer requests a groove be widened by 2mm, a carver can’t be beaten for speed and efficiency. Rolling resistance testing for a tread pattern is a machine-based procedure and as such needs only a single prototype tyre, and here the carving team may also come into action. On-track testing obviously requires a minimum of four tyres, making the decision between carver and robot a more complicated one.
Carving for go & for show
Last year, Continental’s carving team in Hannover-Stöcken produced 1,700 tyres by hand, working on everything from motorcycle to truck tyres. Many of these were prototypes for track and machine testing, but Recker and his colleagues also carve tyres for show. Car makers and other firms occasionally approach Continental and request eye-catching tyres for concept or custom cars that they’re displaying at auto fairs and exhibitions.
Recker and colleague Martin encourage visitors to their workplace to try their hand at tyre carving. German Chancellor Olaf Scholz did so in April, and word is that he needn’t apply for a job once out of office. I also pressed the custom-made knife into a tyre, and while Bardles would likely have been impressed with my handiwork, chances are that Continental won’t invite me to start a new career any time soon. This shouldn’t come as a surprise, as Wolfgang Recker tells us that it takes as long as two years to train a highly competent tyre carver.
Comments