ISCC PLUS certification for Kal Tire recycling plant
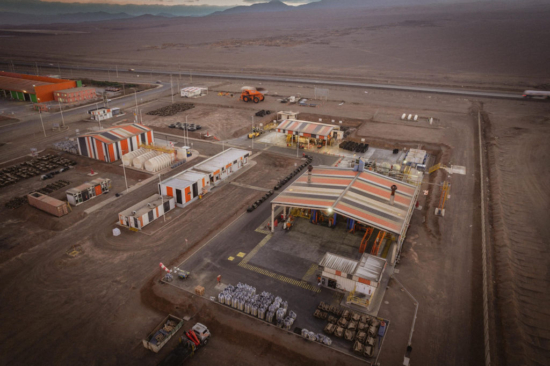
Kal Tire’s Mining Tire Group reports that its mining tyre recycling plant in Chile has gained International Sustainability and Carbon Certification (ISCC) PLUS certification, verifying it meets the circular materials standards for reclaimed oil, carbon black and syngas using a mass balance chain of custody approach. It thus becomes one of just a handful of mining tyre recycling facilities in the world to generate outputs that are 100 per cent ISCC PLUS compliant.
“Kal Tire is committed to promoting a circular economy where recycled mining tire products are given their highest and best use,” says Dan Allan, senior vice president, Kal Tire’s Mining Tire Group. “This ISCC PLUS certification ensures customers can confidently source our recycling facility’s outputs knowing they’re 100 per cent derived from waste materials.”
At Kal Tire’s facility in Northern Chile, end-of-life ultra-class tyres are converted to their base elements of carbon black, oil and steel, ready for reuse in new products in place of raw materials. The facility’s thermal conversion processes utilise heat and friction to induce a process that sees virtually 100 per cent of the tyre reused.
Third-party validation
As more and more organisations look to demonstrate the sustainability and circularity of their supply chain, Kal Tire anticipates that its ISCC-certified products will provide third-party validation for customers seeking sustainable, circular materials.
“Years ago, we set out to invest in a solution at the top of the mining tyre recycling hierarchy to help customers solve the great challenge of handling end-of-life mining tyres more sustainably, at a time when government also began calling for environmental leadership and contribution to climate action plans,” says Allan. “We’re proud to now be at this stage with our certified and high-quality outputs, helping customers create a greener supply chain and a lower carbon future.”
Kal Tire’s facility has the capacity to process five 63-inch tyres, weighing a total of 20 tonnes, each day. The recycling process converts these tyres into 8,000 kg of carbon black, 6,500 litres of oil, 4,000 kg of steel and enough synthetic gas to fuel the plant itself for seven hours. The company is seeing growing demand for recovered carbon black (rCB), which can be used to produce tyres and plastic products.
Comments