Bosch develops fully automated battery-discharging plant
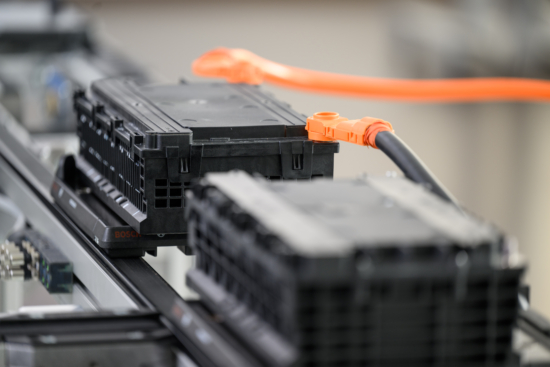
Bosch estimates that electric vehicles will account for around 70 per cent of Europe’s newly registered passenger cars by 2030. And the growing electric v vehicle parc means increasing demand for both new batteries and for the recycled raw materials they contain, such as lithium, cobalt, and nickel. In response, Bosch has developed new machinery, equipment and software for this purpose. Specifically, Bosch subsidiary Bosch Rexroth is supplying Battery Lifecycle Company, a joint venture between Remondis subsidiary TSR Recycling and Rhenus Automotive, with Europe’s first fully automated system for discharging and disassembling battery modules.
“Electromobility can only establish itself in the long term if sufficient raw materials are available for battery production. Recycling plays a key role here, and helps place our output on a sustainable footing: we reuse what we use, and we recover raw materials,” said Dr Stefan Hartung, chairman of the Bosch board of management.
By 2030, Europe will require up to 420,000 metric tons of battery material recycling capacity, according to Fraunhofer ISI. “If we want to build a European circular economy, we need to integrate recycling firmly into the product life cycle and create the necessary infrastructure to do so. Bosch is contributing its technical expertise to this,” Hartung continued ahead of Bosch’s battery recycling presentation at Hannover Messe (17-21 April 2023).
“What we do today sets the course for tomorrow. The batteries currently being installed in vehicles will have reached the end of their life in 10 to 15 years. We must use this window of opportunity to build the necessary recycling capacity,” Steffen Haack, CEO of Bosch Rexroth explained.
According to the Fraunhofer Institute for Systems and Innovation Research, the technical systems required for recycling require investment of more than 6 billion euros by 2040 in Europe alone. But that investment will be able to recover up to 95 per cent of a battery’s chemical elements and recycle them into the battery production process in optimal conditions. Bosch reports that its automated discharging system not only simplifies recycling, but also increases efficiency and enhances safety. Indeed, it takes just a few minutes to deep-discharge a module. The system recognizes different battery designs, minimizing risks such as short circuits and fires.
Model project at Battery Lifecycle Company
Battery Lifecycle Company is building Europe’s first fully automated plant at its site in Magdeburg, with Bosch Rexroth supplying the technology. The site will test used batteries from different manufacturers, deep-discharge them, and prepare them for subsequent shredding. The new plant’s workpiece carriers will each transport battery materials weighing up to 150 kilograms at a speed of 18 meters per minute. This means that it will take less than 15 minutes to automatically discharge eight lithium-ion batteries from electric cars. Bosch’s automated solution will greatly increase the speed of recycling: with the manual process currently used, it takes up to 24 hours to deep-discharge a battery. The model project in Magdeburg is the first to use this patented Bosch discharging solution: battery modules will be chemically deactivated in a reliable process, ensuring that further processing can take place without voltage. The residual energy in the modules can be used to operate the recycling system. In addition, the site will use proven Bosch industrial technology for battery production on-site, including flexible, modular transfer systems and the ctrlX AUTOMATION control platform. Each year, the Battery Lifecycle Company site will recycle up to 15,000 metric tons of battery materials. The plant is scheduled to go into operation in summer 2023.
Bosch has many years of experience in the development of automation and manufacturing technology for battery production. All the premium German automakers and many battery production facilities worldwide use Bosch industrial technology. Bosch is continuously expanding its portfolio along the value chain for battery production. The company has now developed hardware and software specifically for battery recycling, which is marketed worldwide together with partners and system integrators. In addition to fully automated battery module discharging stations, these include ergonomically flexible workstations for technical analysis and safe battery disassembly, transfer systems for transporting batteries of different weight classes, and software for guiding workers through the various process steps. Bosch also offers a track and trace solution for the condition, material origin, and processing status of batteries.
Comments