Zeppelin Systems & its tyre recycling partners
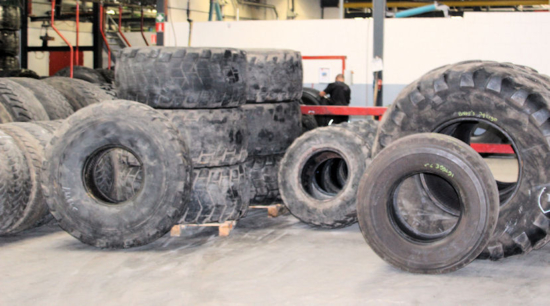
As Tyrepress reported on 21 March, Zeppelin Systems has recently entered into a number of partnerships in the area of tyre recycling. It considers these firms key players in its new circular economy endeavour, the Zeppelin Sustainable Tire Alliance. Partners include Polish companies ReOil and Rezykl, France’s Regom, Italian technology group RubberJet & Vertech and German firms Entex and RCB Nanotechnologies. Zeppelin Systems has shared some details about its new partners:
Entex
ENTEX Rust & Mitschke GmbH is the leading manufacturer of planetary roller extruders and has over 160 intellectual property rights registrations to its name since its founding. The specialist talent Entext brings to the Zeppelin Sustainable Tire Alliance is the devulcanisation of waste tyre rubber using its planetary roller extruder.
RCB Nanotechnologies
RCB Nanotechnologies specialises in the finishing of raw-recovered carbon black, and Zeppelin Systems thus believes the company “perfectly complements” its “wide range of services throughout the sustainable circular economy for the tyre industry.”
With the tyre industry utilising around 70 per cent of global carbon black production, and 1.5 tonnes of fossil raw materials and large amounts of water needed to produce a tonne of virgin carbon black, Zeppelin Systems sees great potential for processes that glean rCB from end-of-life tyres, with around three kilogrammes of carbon black locked up in a typical scrap car tyre. “We want to offer our customers sustainable alternatives for tyre production – with consistent quality and in sufficient quantity,” comments Guido Veit, Zeppelin Systems’ vice president sales for Polyolefins, Rubber and Silos. This is where RCB Nanotechnologies steps in.
RCB has Nanotechnologies developed a process in collaboration with the Fraunhofer Institute for Building Physics IBP that separates the ash content (of up to 25%) from the rCB obtained by pyrolysis. The results, note Zeppelin Systems, are a “high-quality and extremely pure” rCB.
Numerous tests with well-known tyre manufacturers confirmed that the rCB quality is “absolutely comparable to the original industrial material” (for example, N660 or N772) and therefore can entirely replace certain standard carbon black grades in future. In addition, other high-quality products are obtained in the process, such as silicon- or zinc-based compounds, creating further, sustainable material cycles in the process for the construction and tyre industries.
Recykl
Starting 3 February 2023, Zeppelin Systems is partnering with the Recykl Group, an established Polish market leader in the management of post-consumer waste in the form of end-of-life tyres. Sharing news of the arrangement, Zeppelin Systems states that “the strategic merger of the two companies generates valuable synergetic effects in the development and marketing of technologies in the field of end-of-life tyre recycling.”
Recykl Organizacja Odzysku S.A. is part of a large capital group (Recykl Group, GRC) and been intensively engaged in the reprocessing of used tyres since 2004. The company processes over 120,000 tonnes of used tyre material every year, making it one of the largest companies of its kind in Central and Eastern Europe.
According to Zeppelin Systems, the merger with Recykl Group takes the mechanical recycling of used tyres to the “next level.” Plant engineering technology is provided by Zeppelin Systems, while the Recykl Group provides the process for tyre recycling, in particular the devulcanisation of rubber. The result is high-quality recyclates that can be directly integrated back into the production cycle for new tyres.
This new partnership represents an “important alliance” for Zeppelin Systems: “As an integrated solutions provider for the recycling of end-of-life tyres, we are closing an important gap in the circular economy by means of our partnership with Recykl Group,” says Guido Veit. “We are making our contribution to commercialising the recyclate production technologies which the tyre industry urgently needs to manufacture sustainable tyres.”
Regom
French company Regom, which specialises in sorting scrap tyres using artificial intelligence (AI), joined the alliance on 10 February 2023.
Every three seconds, a fully automatic Regom tyre sorting machine determines the future of a used car tyre, with the fate of around 800 tyres sealed after an hour of operation. Such speedy sorting is possible with the help of AI, which evaluates tyre sidewall images at lightning speed after measurement and determines exact features and further use of scrap tyres. Tyre brand, model, dimensions and wear are detected with high levels of accuracy. “This process step is very important for the further processing and high-quality recycling of scrap tyres,” comments Veit. “At the same time, the workload in tyre sorting is greatly reduced because tyres no longer need to be sorted and evaluated manually.”
Veit adds that a further advantage exists for the second-hand tyre market in that “the exact measurement and evaluation automatically increases the proportion of recyclable tyres.” Tyres that are not suitable for further use are mechanically separated and shredded as the next step. Due to the high degree of precision in the sorting process, the quality of the resulting recyclates increases in terms of their grade purity, creating a “perfect starting point for manufacturing new tyres with recyclates from used tyres while also supporting the circular economy.”
In addition, Zeppelin Systems points out that AI-based scrap tyre sorting can be easily integrated into existing recycling systems and is therefore a “perfect addition” to its tyre recycling services.
ReOil
Joining the alliance on 13 March 2023, Poland’s ReOil operates in the area of raw material recycling and breaks down used tyres into raw materials such as steel, oil and recovered carbon black (rCB) by means of continuous pyrolysis. Founded in 2010, the company built Europe’s largest pyrolysis tyre recycling plant in the city of Bukowno in 2015. Since then, the facility has recycled around 20,000 tonnes of used tyres every year, and another plant that will triple capacity to around 60,000 tonnes is now in the planning phase.
Rubberjet & Vertech
With a partnership that began on 7 February 2023, Zeppelin Systems is now working with the Italian firms RubberJet and Vertech, which specialise in recycling end-of-life tyres from trucks, construction and mining vehicles. Their patented process breaks down tyres of up to four metres in diameter into individual parts via a high-pressure water jet process. This separates rubber and steel, and the rubber powder and granulate obtained can be marketed directly as recycled material.
By their very nature, the high natural rubber content of rubber used in large tyre compounds ensures that the recyclates obtained are of particularly high quality. In addition, the recycling process gives the recycled materials an especially large surface structure. This is essential for renewed interlacing, which influences the recycled material’s revulcanisation within new tyre compounds or new rubber compounds.
RubberJet Group has been in business since 2016, and the Italian company invested over six years developing the patented and proprietary waterjet technology. “With High Pressure Water Jet Technology, large tyres can be economically and resource-efficiently recycled into a high-purity and surface-activated rubber powder that can be directly reused in a rubber compound,” says Guido Veit.
Comments