Pyrum Innovations founder: “Our pyrolysis works”
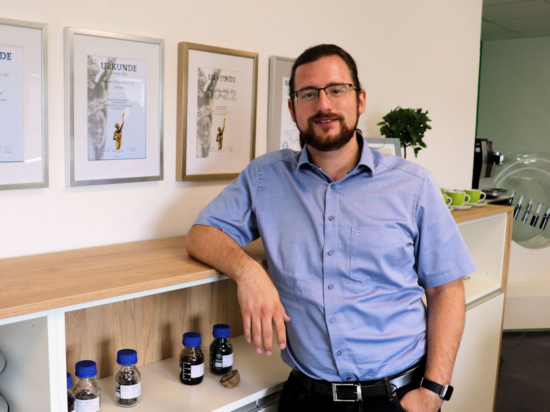
Landfills are a no-no, so other solutions must be found for the billion tyres reaching the end of their useful lives worldwide each year. And although the cement industry is a major customer for these end-of-life tyres, countries such as Sweden, Finland, Belgium and Norway have already banned the burning of tyres in cement kilns, and others will certainly follow suit. So if we can’t bury them and we can’t burn them, what do we do with these waste tyres? Pyrum Innovations is showing the world its solution, and customers, project partners and suppliers are already lining up to be part of it.
Michelin, Continental, Schwalbe, BASF – this shortlist of partners and investors nicely illustrates the company that Pyrum Innovations AG keeps. But what makes this firm – just 14 years young – so attractive to such major, well-known partners?
Pascal Klein has a ready answer. The co-founder and current chief executive officer of Pyrum Innovations says his company operates the only fully functional pyrolysis plant in Europe. This has run reliably around the clock since May 2020 and produces products of consistently high quality. Explained simply, pyrolysis is the heating of materials, in this case waste tyre granulate, and the exclusion of oxygen in order to produce oil and gas as well as coke. This in turn can be further processed into recovered carbon black (rCB); more on this later.
Advantages of vertical reactor
The core of the Pyrum thermolysis process is the vertical reactor that turns granulated scrap tyres into oil, gas and, carbon black (Photo: NRZ / Arno Borchers
Pyrum Innovations relies on its patented vertical reactor, whereas other companies engaged in pyrolysis usually employ rotary kilns that – according to Pascal Klein – are “never impermeable” due to their rotation and therefore work inefficiently, not delivering the consistently high product quality demanded by customers. In addition, the process offers another specific feature: After using an external source of energy for the initial start-up, the plant supplies enough gas to ensure its “self-sufficient operation” via the combined heat and power plant, which in turn is operated with pyrolysis gas, whereas gas resulting from rotary kiln pyrolysis often must be flared off.
Pyrum Innovation’s 36-year-old founder and chief executive officer did not follow a conventional career path to get where he is today. He tells us that during the course of his business studies (which he later completed), his father introduced him to “inventor and thoroughbred technician” Klaus-Peter Schulz, who was looking for an investor for a “new type of pyrolysis that had never existed before” but which he’d already been “tinkering with for over 20 years.” Klein recalls that Schulz had realised rotary kiln pyrolysis would not deliver the desired results, and he had therefore discarded the technology “in favour of a new type of pyrolysis.”
Klein was tasked with conducting patent law research for his father, a self-employed entrepreneur from the small German town of Dillingen/Saar who was keen to invest, and potentially drawing up a business plan based on this. It took Pascal Klein and three of his fellow students a good year to conclude that the concept “has potential” and “could be something.”
Gradual development of ecological drive
Since the inventor Schulz was not interested in investing, he sold Pascal Klein and fellow student Julien Dossmann his clearly patentable idea. The students founded Pyrum Innovations ESC GmbH in 2008. The company name, which Klein shares was coined “in grandpa’s wine cellar,” is a made-up word that stands for pyrolysis, recycling and environmental protection. The founders’ initial capital amounted to 340,000 euros, including 140,000 euros from a development loan from France, where the company was originally based. But 340,000 euros is not a lot of money, even when using just a small pilot plant to demonstrate the new process (known at the time as thermolysis) for potential investors and customers. Pascal Klein and his partners recall difficult years for the young start-up company, frequently plagued by financial concerns.
For Pyrum’s founder, the original motivation was not to improve the world or to pursue any kind of ecological mission. Blessed by nature with the ‘self-employment gene’, Klein comments that a nine-to-five job always seemed “like a nightmare” to him. And although taking over his father’s company would have seemed the obvious career path, Klein viewed this as a “system” that he wished to “escape”, especially in his young student years.
Monetary considerations also played a central motivational role in the early days for Klein and his co-founders; how could it not when they were “chronically broke”? But this changed with each further developmental step the company was able to take, Pascal Klein recalls. “The older you get, the greater the moral pressure to do something good becomes,” he adds. This became the “ecological drive” behind Pyrum.
Diverse & growing service
The service that Pyrum Innovations now provides and markets is extremely diverse and currently on the verge of a large-scale breakthrough. Following its founding in 2008, Pyrum commissioned a pilot plant in 2009. This was followed in 2016 by an industrial-scale facility for the recycling of up to 5,000 tonnes of scrap tyres annually. The scrap tyres recycled in this plant, which incidentally are prepared for the process in a dedicated shredder capable of handling tyres up to 1.2 metres in diameter, are processed into recovered tyre carbon black (rCB). The pyrolysis process results in 25 to 40 per cent thermolysis oil, 40 to 45 per cent thermolysis carbon black and ten to 25 per cent thermolysis gas.
However, this carbon black – a powder in the order of ten micrometres or smaller – has so far only been marketed to manufacturers of so-called virgin carbon black (vCB), explains Pascal Klein. These manufacturers, who in turn supply the tyre industry, mix the rCB with the vCB in limited quantities, although as its name suggests, the vCB is actually 100 per cent based on crude oil.
As part of a European Union project commenced in 2020, Pyrum pyrolysis oil is processed into carbon black by Orion Engineered Carbons and then used in tyre production by Michelin, which leads the 13-participant BlackCycle project. The project doesn’t focus upon mixing in a recycled material in small quantities – on the contrary. Initial tests show that the raw material, which is then called sCB (sustainable carbon black), has “identical properties to conventional carbon black of the same quality,” which “impressively demonstrates the suitability of the product for the complete substitution of fossil raw materials.”
At present, however, Pyrum Innovations is starting to supply tyre manufacturers directly with rCB. To this end, the company installed and commissioned a pelletising plant in May to ensure it can meet the industry standard for the correct grain size: Manufacturers need their tyre carbon black as pellets or beads in the order of one to two millimetres and not in powder form in the micrometre range.
But here too, says Klein, the recycled raw material can often only be added to vCB. Whether and to what extent this is possible depends on which part of a tyre is made from the material; it is a question of mixing qualities, conditioned by the purity of the raw material used.
Klein’s recipe
The rCB produced by Pyrum in Dillingen/Saar is and remains a recycled raw material suitable for use in a wide variety of tyres, from truck to car and motorbike tyres. To create a certain consistency amongst the input materials and thus the final rCB, Pyrum Innovation’s shredder and thermolysis plant is always filled according to the same recipe: 55 per cent car tyres and 45 per cent truck tyres, based on weight.
According to Pyrum, such a scrap tyre mixture and the carbon black recovered from it can usually completely replace vCB of quality level N600. Pascal Klein says it is easy to explain why there is such a huge demand for the Pyrum recycling raw material. While N600 vCB in pellet form recently cost tyre manufacturers about 1,500 euros per tonne, the calculation for Pyrum’s own and pelletised rCB comes at a price of only 750 euros.
However, N600 “only” represents about 20 per cent of the vCB that the tyre industry processes; it is used in inner liners, for example. With better and correspondingly more expensive qualities such as N300 or even N100, carbon blacks used for safety-relevant tyre treads that require precision when compounding, substitution is only possible to a limited extent. “Even if rCB can never completely replace virgin carbon black,” the Pyrum founder and chief executive officer stresses that thanks to the aforementioned savings potential, the entire industry is currently researching how to maximise the volume share of the recycled raw material.
But beyond economic motives, tyre manufacturers are driven by obvious ecological benefits that also in turn benefit their OEM partners, the vehicle manufacturers, not to mention the environment itself. Demanding targets related to sustainability, reducing CO2 emissions and recycling are being formulated or codified at all economic and political levels. In order to achieve the corresponding ecological goals, the proportion of circular or reused raw materials must increase continuously, and significantly. The motivation on the part of tyre manufacturers and their OEM customers to make a contribution through the use of thermolysis products, and not only in tyres, is therefore great.
Pyrum products in Mercedes cars
The company from Dillingen/Saar recently announced that its partner and major shareholder BASF (which holds 7.9 per cent of Pyrum shares) supplies Mercedes-Benz with plastics that are produced from Pyrum pyrolysis oil and processed into vehicle components (see separate text). According to Pascal Klein, many other (potential) customers are “queuing up for us,” and what’s more, Pyrum is “overwhelmed with enquiries.”
But will Pyrum Innovations be able to save the world from its waste tyre problem? This is hard to imagine when looking at the recycling volumes that Pyrum Innovations can currently process. The firm’s industrial-scale plant has a capacity to accommodate 5,000 tonnes of used tyres per year. The former pilot plant is still on site but no longer used. To address capacities, Pyrum Innovations is investing heavily in the expansion of its central site, building two new vertical reactors with an annual capacity of 7,000 tonnes each, another shredder/granulator and another pelleting plant. The total cost of this project is 25 million euros.
But that is not all. As the company has announced in presentations, several more scalable thermolysis plants are currently in the planning stage, either together with offtake partners or directly, (see accompanying article). “In the long term,” according to company reports, the construction of 23 Pyrum plants is on the agenda. “We need to build more Pyrum plants. Because our pyrolysis works,” concludes Klein.
Comments