Pro-Align: cost of living vs cost of life
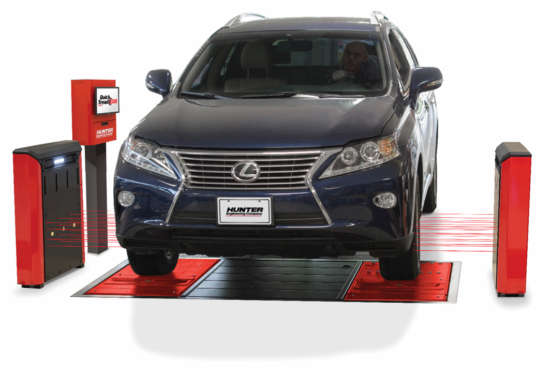
Hunter’s latest drive-over equipment offers automatic checks to identify service requirements more efficiently, while EV growth offers opportunity for cutting-edge wheel balancer
Pro-Align’s Quick Tread Edge has joined the Quick Check Drive in offering garages the opportunity to identify servicing opportunities with great speed and efficiency, while also offering a customer-friendly interface designed to support businesses’ relationship with their customers. The exclusive distributor of Hunter garage equipment also explains how electric vehicles are increasing the need for accurate and efficient wheel balancers.
With drivers’ pockets being squeezed by the cost of living crisis, garages’ customer relationships have arguably never been more important. Ensuring that customers are well-informed and feel their money has been well-spent plays a huge role in securing repeat business. Garages need to ensure budget restrictions inevitable in the current economic climate do not mean safety becomes a secondary consideration. Workshops have a duty of care to their customers to remind them of the legal parameters that exist to keep everyone on the road safe, not just them.
Pro-Align therefore urges garages to “think about safety and not the sale.” For example, having wet weather braking distances to hand will also serve as a physical reminder of the potential implications of not having safe tyres fitted to a vehicle, which could indeed make a hypothetical situation become real. If a customer does not receive this advice from a professional workshop, then they are unlikely to have the opportunity to benefit until a next service is due. The garage equipment distributor likens the customer’s visit to the garage to a visit to their doctor for a diagnosis – “both scenarios have the potential to save lives.”
TyreSafe research recently found more than 70 per cent of tyres on the road have a tread depth of 2mm or below, while more than a quarter were below the legal limit of 1.6mm. This highlights the unawareness of many drivers of the dangers of tyres with very low tread depth, as well as implying they cannot afford to replace tyres proactively when required. Showing customers what is required to keep their cars safe in a professional and clear way increases road safety while supporting garages’ revenues. While there are many tools that can analyse the health of a vehicle’s tyres, Pro-Align questions whether they can they do it “as fast as the Quick Tread Edge drive-over system from Hunter.”
The Quick Tread Edge wheel diagnostic drive-over health check system automatically measures the tread depth and wear of each tyre from edge to edge in between three and seven seconds. This not only helps workshops to sell more tyres but also keep their customers informed about the health of their tyres and when they might need to look at a replacement, Pro-Align says. Furthermore, the advanced system helps technicians highlight any excess tyre wear – a common issue caused with misalignment.
The innovative system’s cloud-based software, HunterNet, provides a wealth of reporting and management information designed to improve customer service and maximise workshop profitability. Quick Tread Edge provides instant access to tyre tread analysis with results displayed both directly on screen or via print out, allowing technicians to clearly highlight any tyre wear and safety issues to the customer.
‘Quick Check Thrive’
Hunter’s drive-thru wheel alignment inspection system, Quick Check Drive, is capable of automatically conducting an alignment check in three-to-five seconds. When situated at the front of a workshop alongside the Quick Tread Edge, businesses have the power to identify a host of revenue opportunities without having to lift a finger. This opportunity can harness incredible benefits, Pro-Align explains. Wheel alignment servicing “typically offers profit margins of around 88 per cent,” it states, adding that “an estimated seven in 10 cars on the road have some form of misalignment.”
Figures from Hunter show that workshops using these systems are finding that more than 70 per cent of the vehicles they check have some form of wheel alignment issue, while at least half of the vehicles scanned showed excessive tyre wear or other tyre related problems. Not only are these workshops able to create more paying jobs from these drive over systems, but they are also improving customer satisfaction and potentially securing a long term, trusted clientele, Pro-Align adds.
- Hunter Road Force Elite (Photo: Pro-Align)
- Hunter Road Force Elite (Photo: Pro-Align)
EV wheel balancing offers increased opportunity
Society of Motor Manufacturers and Traders (SMMT) data shows three quarter of a million electric cars, vans, buses and trucks were on the road in 2021. With EV usage growing, workshops must be equipped with the right tools and technicians trained, in order to address a host of new servicing challenges. While much focus and attention is on the vehicle’s electronic architecture, workshops should also consider new challenges associated with traditional components, Pro-Align says.
“As part of the EV revolution, workshops will undoubtedly see more customers who have concerns about vibration issues,” explains Clive Seabrook, CEO of Pro-Align. “Replacing an internal combustion engine with an electronic drivetrain means that drivers will be much more aware of other vibrations, such as those from wheel and tyre assemblies, that would previously have been masked by those coming from the engine. Consequently, workshops need to prepare for this with equipment that can diagnose and solve these issues efficiently and effectively.”
Hunter Road Force Elite (Photo: Pro-Align)
Pro-Align offers the Hunter Road Force Elite (RFE) diagnostic wheel balancer as a solution. Older wheel balancer technology is unable to solve the most challenging and subtle wheel vibration issues other than by trial and error – often a costly process in terms of weights and labour.
The balancer offers a unique diagnostic approach, Pro-Align says. The RFE can provide a fast, first-time fix to any wheel-vibration problems, even doing so in less time than a standard wheel balancer.
The RFE differs from standard balancers as it measures tyre forces known as Road Force Variation (RFV) and Lateral Force (LF) to conduct a full diagnostic of the wheel and tyre assembly. It does this by scanning the wheel rim and applying a load via a roller to take the wheel and tyre assembly on a simulated road test.
Once RFV is identified, the balancer provides a ‘ForceMatching’ recommendation which matches the stiff spot on the tyre with the low spot on the wheel rim, minimising any vibrations to give a smoother ride. Where LF is identified due to conicity of the tyres, the RFE even advises of the best position on the vehicle to counteract it for a straighter drive.
A better ride
“Undoubtedly, motorists are going to become more demanding of workshops with regard to wheel vibration issues,” adds Seabrook. “Of course, this isn’t exclusively an EV issue as ride quality continues to improve on all cars. Thankfully though, we’re delighted that once again, the insightful engineers at Hunter have been among the first to identify this future problem and develop a solution that will help workshops provide their customers with the very best levels of service.”
Comments