Goodyear EMEA reducing tyre production, exiting TrenTyre after third-quarter operating income fell $51 million
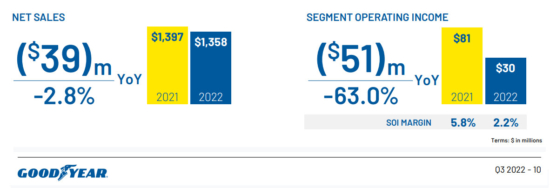
Goodyear’s latest financial results show that third-quarter 2022 group sales grew 7.6 per cent to $377 million up from $5.311 billion and $4.934 billion respectively the preceding two years. According to the company, the increase was driven by pricing actions that drove revenue per tyre (excluding foreign currency) 16 per cent higher than Q3 2021 level. At the same time, sales were impacted by lower tyre volumes, which declined 3 per cent.
However, the figures were less positive on this side of the Atlantic and net sales in EMEA (the Europe Middle East and Africa region) decreased $39 million, or 2.8 per cent. The sales decline reflects 6.5 per cent lower unit volumes and a 22 per cent negative impact of currency devaluation, partly offset by a 17 per cent increase in revenue per tyre.
Meanwhile, EMEA third-quarter operating income totalled $30 million compared with $81 million a year ago – a decrease of $51 million. Energy costs, which equated to a $33 million “unfavourable impact” and the cost of lower volumes in the quarter was ($21 million) won’t have helped the situation.
One interpretation of the data is that Goodyear is struggling with overcapacity in Europe, something that is demonstrated by recent plans to close the Cooper Europe Melksham, UK tyre factory and the merger of motorcycle tyre capacity in Montluçon, France.
As a result of those changes, Goodyear executives expect to record pre-tax charges of between $80 million to $90 million, of which $60 million to $70 million are expected to be cash: “We expect most of the cash outflows associated with this plan to occur in 2023”, executives wrote, emphasising: “The plan remains subject to consultation with relevant stakeholders.”
There are also plans to exit the TrenTyre retail operations in South Africa. Total expected expense and cash charges from this plan amount to $18 million. Taken together, the full run rate savings for these plans are expected to be approximately $30 million by 2024.
The next “rationalisation” step is to “reduce production by approximately 10 days [and circa 1.5 million units] at most of our European factories in order to address softer demand and prevent the build-up of excess inventory”, according to the latest investor letter.
Other efficiency steps include: action to help address shortages energy conservation and energy efficiency projects.
Comments