Mercedes-Benz using ‘tyre plastic’ in vehicle production
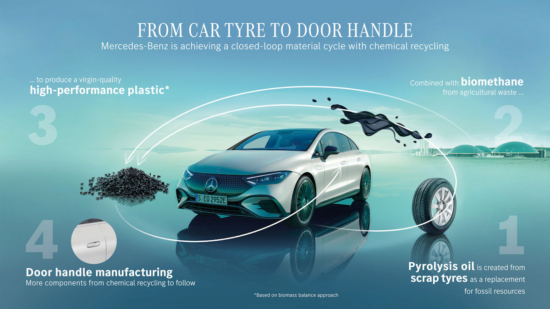
Discarded tyres will soon find a new home within the latest Mercedes-Benz models. Pyrum Innovations AG, which produces pyrolysis oil from end-of-life tyres (ELT), is supplying oil to its cooperation partner BASF SE, which in turn is combining the oil with biomethane as a raw material in the production of virgin plastics for vehicle components. Door handles will be the first products to have their fossil raw materials replaced by biomethane and pyrolysis oil from ELT. These will appear on Mercedes-Benz EQE and S-Class models later in 2022.
“Through close collaboration with our supplier network, we are replacing raw fossil resources with pyrolysis oil made in part from recycled scrap tyres supplied by Mercedes-Benz. Components featuring this technology will enter series production in a number of our models as soon as this year,” says Markus Schäfer, chief technology officer and Mercedes-Benz Group Board of Management member responsible for development and procurement. “We anticipate being able to chemically recycle several hundred tonnes of scrap tyres from Mercedes-Benz vehicles every year and use the resulting plastic in our new vehicles. Together with our partners, we are closing the materials loop and actively driving the development of innovative recycling processes.”
“Since the foundation of Pyrum, we have been working on getting closer to a circular economy step-by-step,” adds Pascal Klein, chief executive officer of Pyrum Innovations. “In view of finite deposits, the aim can only be to minimise the consumption of natural resources and to use as much recycled raw material as possible in production. The fact that our pyrolysis oil is used as a basis for the production of Mercedes-Benz vehicle components shows the high quality of our products.”
Independently certified
Pyrum pyrolysis oil will be fed into the BASF network of ‘Verbund’ production sites at the start of production. Combining this raw material with renewable biomethane from agricultural waste results in a completely new plastic that is now being used for the first time. This plastic is certified according to the ‘mass balance method’: An independent certification confirms that the quantities of fossil resources required for the end product have been replaced with renewable raw materials and pyrolysis oil from ELT.
In addition to reducing both fossil resources and the CO2 footprint in the manufacturing process through the use of secondary materials, Pyrum emphasises that the recycled plastic has the same properties as virgin plastic made from fossil raw materials. It thus considers chemical recycling to be particularly suitable for the production of components that are subject to high quality and safety requirements.
Significant potential
Mercedes-Benz states that as the plastic shares the same characteristics as virgin plastic produced from crude oil, reduced carbon footprint and fossil resource usage are not the only benefits – the material also fulfils its quality demands, especially in respect of paintability and crash safety. “These properties mean the process has the potential to replace a large number of vehicle components made from primary plastic,” states the vehicle manufacturer.
In addition to the aforementioned door handles, Mercedes-Benz will also equip the S-Class with a crash absorber made from the recycled plastic material. The vehicle manufacturer is currently exploring further possible applications for the recycled material as part of its goal of increasing the proportion of recycled materials in its car fleet to an average of 40 per cent by 2030.
Comments