Wastefront partners Newcastle University in recovered carbon black study
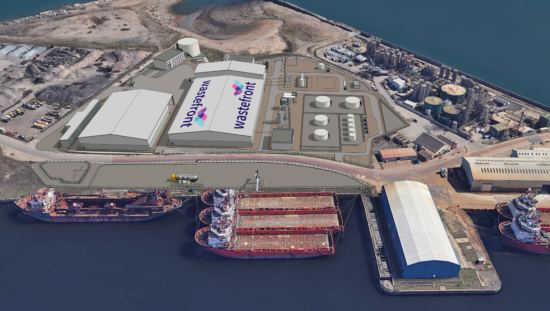
World-leading university in sustainability partners with cutting-edge Nordic circularity company to undertake 18-month research study
Wastefront and Newcastle University have formed a partnership to enhance the recycling firm’s recovered carbon black (rCB). The university is a globally recognised leader in sustainability research, and will help the cutting-edge tyre recycling company complete an 18-month study to develop innovative industrial solutions for Wastefront’s first tyre recycling plant in Sunderland. The partners state that they want the North of England to be at the forefront of progressing circularity across Europe.
The study will focus on rCB interaction with rubbers and its correlation with prospective industrial applications, directly supporting Wastefront’s efforts to enable the rCB it produces to be used in new products. The scope of work undertaken by Newcastle University over the next 18 months will:
- Quantify the interaction of the rCB with a set of different solvents which have varying degrees of dispersion interaction.
- Develop methods to better understand the nature of the surface within the rCB material.
- Investigate applications for the rCB in other materials.
Wastefront AS CEO Vianney Vales at Port of Sunderland with Cllr Graeme Miller (Photo: Wastefront)
Of significance, within this scope of work, the study will develop methods to reduce inorganic components in rCB, improving its chemical and material properties to ensure Wastefront produces a superior product compared with its rCB competitors. This will include identifying rCB reinforcement in rubber goods.
The team from Newcastle University undertaking the rCB study will be:
- Professor Katarina Novakovic – principal investigator, reader in polymer engineering
- Professor Steve Bull – co-investigator, cookson group chair of engineering materials
- Dr Deepashree Thumbarathy – post-doctoral research associate, chemical engineer
- Dr Tim Blackburn, business development manager
Wastefront CTO, Henrik Selstam, comments: “Circularity is central to the work Wastefront is undertaking to tackle the scourge of ELTs – and expanding our understanding of recovered carbon black is key to realising this goal. As we continue to grow, so too will the uses and capabilities of the products we produce – none more so than recovered carbon black.
“We are delighted to partner with Newcastle University to further advance the commercial capabilities of recovered carbon black through our joint studies. “Ensuring we can continue to implement our at-scale solution in the UK, Europe and Globally will require the input of leading experts in their fields, so we look forward to working closely with Professor Novakovic, Professor Bull, Dr Thumbarathy and Dr Blackburn in the months ahead.”
Newcastle University pro-vice-chancellor for research strategy and resources, Professor Brian Walker, adds: “At Newcastle University we are delighted to add this exciting partnership with Wastefront to our portfolio of research that advances sustainable innovation and the circular economy and enables progress towards a net-zero economy. We are especially pleased that Wastefront will promote inclusive economic growth here in the North East, with its roots in the local area and the construction of its new plant at the Port of Sunderland.”
Wastefront says it will play a crucial role in eliminating the UK’s waste tyres export. It wants to create a local, circular solution to the global problem of how to improve the recovery of energy and materials from ELTs. Through preventing the burning of waste tyres in cement kilns, Wastefront will use commercial operating technologies to convert end-of-life-tyres (ELTs) into useful commodities including rCB.
Wastefront uses pyrolytic reactors that utilise thermal depolymerisation, popularly known as “pyrolysis”, to break down a tyre’s materials at elevated temperatures. By sending tyres through these reactors, recovered carbon black (a substitute for virgin carbon black) is produced, in addition to combustible gas, liquid hydrocarbon, and heat. The carbon black is then washed and milled to upgrade the chemical properties and can be used as a complement to natural rubber in tyre production, mechanical rubber goods or as a filler for plastics.
Once fully operational in 2025, Wastefront’s £100 million tyre recycling plant in Sunderland will produce rCB from a supply of 20% of the UK’s yearly total of ELTs. By integrating Wastefront’s rCB into new tyres, the emissions for each tyre subsequently produced will be reduced by 80 per cent.
Comments