Alba Tyres Management: Premium approach and Marangoni Ringtread partnership key to growth
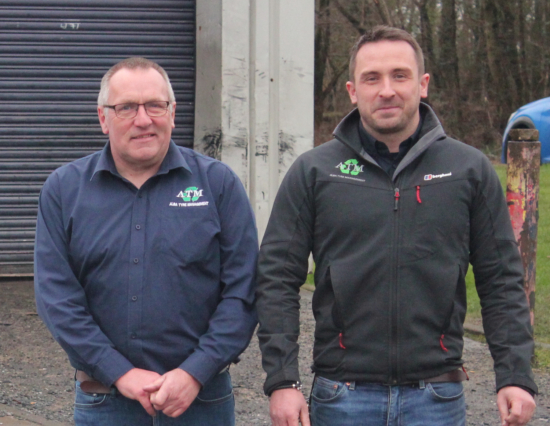
Not far outside Glasgow, Alba Tyres is taking on an increasingly influential position in the Scottish retreading business. The company has got there by virtue of the combination of a sharp focus on its core business and an increasingly efficient – and technologically driven – production process. Tyres & Accessories took the high road to Scotland to meet directors Alex and David Wilson to find out more.
It all started in the summer of 2004 when Alba Tyre Management was founded by directors Alex Wilson and Michael Proctor and since 2013 grow into a wholly family-owned business. The founders brought with them a wealth of experience. In particular, Alex Wilson spent the best part of 23 years at McConnechy’s where he got a unique insight into the sharp end of tyre management.
The current retread operation began in the same location in Kilbirnie where the business continues today, but there are a number of differences now compared to how things began some 18 years ago. The most noticeable change is the scale. The current operation covers double the area of the initial set-up, but it is also far more efficient than those early days and the technology has also been significantly upgraded.
From the outset, Alba Tyres’ partnership with the Marangoni RingTread technology has been a key part of both the firm’s production and marketing strategies. Indeed, the combination of Ringtread logo and colours on Alba Tyres’ corporate identity demonstrates the close working relationship between the two companies.
To start with, the company served customers in need of mainly tipper tyre fitments, but over the years the clientele have broadened along with Alba Tyres’ product range. As a result, the company now offers regional and long-haul alternatives as well.
Son David Wilson joined the business in 2005 and is now director of operations at Alba Tyre Management – a role which has enabled him to be a driving force in the perpetual improvement of the company’s manufacturing process. But he didn’t start at the top. Rather, David Wilson has worked in every job in the factory since he started 17-odd years ago.
The truck tyre price war that characterised the early part of the last decade provided the impetus for Alba Tyres to go all-out as a premium player. That season also saw the company invest heavily in training, machinery and lean manufacturing processes. According to the Wilsons, those moves were costly initially but have paid dividends over time.
David Wilson became operations director in 2012 and it was at this point that the factory’s moves in a more technological direction got a real push. Compared to what went before, the Alba Tyres operation is said have had a real face-lift. At the same time, strategically speaking, the factory moved from simply making tyres towards making tyres according to purpose and according to order. That level of focus means the company is now able to produce small lots of exactly the right kinds of targeted tyres, with lots reaching from 36 tyres to as few as three.
While lots of things have changed over the decades, 18 years after the business got going Alba tyres retains the same core staff it had back then. The difference is that they have all up-skilled to keep pace with the latest technologies and developments at the factory. At the same time, new starts have also joined the team and been provided with the environment necessary to grow with the business.
2015/2016 saw Alba Tyres work with Marangoni to introduce the top-end Blackline compound to the company’s portfolio, something that has been ably deployed in the company’s regional and long-haul truck tyre line-up.
One of the obstacles the Alba Tyres team are working to overcome moving forward is the degree of reticence experienced when talking to some hauliers about choosing retreads. As those in the trade know, premium retreads are meticulously remanufactured to offer as-new performance levels and yet some truck tyre customers still argue that the point of entry of some cheap Chinese tyres is lower. However, once fleets have had the experience of working with quality retreads, they often see the benefit. For those wondering what the specific benefits of high-quality retread might be, Alba Tyres point to real-world examples where tyres have travelled 288,000 kilometres on retreads at 50 per cent the price of new premium tyres and all the time utilising 65 less litres of oil.
Promoting sustainability means retreading is the only viable option. So, fleets that want upgrade that sustainability status have to adopt a pro-retread policy. And, as a result, fleets are beginning to ask about this. Moving forward, the target is to raise awareness amongst small and medium-sized fleets whose policies are more about consuming tyres rather than gaining efficiency and sustainability.
With Ringtreads at the core of Alba Tyres’ production process, Marangoni’s Ringbuilder 3000 quickly and accurately retreads tyres (Photo: Chris Anthony; Tyre Industry Publications Ltd)
In order to achieve the necessary awareness-raising amongst small and medium-sized fleets, the Alba Tyres team mainly work with tyre service providers. However, sometimes they use the platform provided by particular events to communicate the benefits of high-quality retreads directly end-users – always referring to and recommending the service provider. The result of this kind of forward-thinking approach is that 50 per cent of Scottish local authorities’ tyre needs are taken care of by Alba Tyres via various tyre service providers.
In addition to standard truck tyre retreading operations, Alba Tyres offers a number of extra services. For example, major repairs represent a significant part of the business. And offering reinforced sidewalls on certain products – such as on/off-road and bus applications – bring with them the chance to position the Alba brand on the sidewall with the inherent marketing opportunity that presents.
Premium quality production = premium quality retreads
Walking around the Alba Tyres factory illustrates how the company’s high quality retread production philosophy is backed up by top-level technology. This combination of bought-in equipment as well as some smart in-house decisions is what results in the retreaded tyres the company is known for.
As you would expect, the production process begins will visual inspection. As well as the obvious condition requirements, this provides the opportunity to check sizes and DOT codes. Alba Tyres added shearography to this process in 2015, something that is said to have brought with a demonstrable return on investment owing to the fact that it ensures the quality of incoming casings and greatly reduces wastage due to issues revealed during the production process.
Next up is buffing where two Marangoni Leonardo Rasp 2500 automated machines operate according to up to 40,000 different buffing programs. The quick release station that forms part of this machine both increases the rate of buffing and ultimately means that the factory’s two buffing and three skiving stations can be manned by two to three operators.
Of course, beyond buffing and preparation lies the building part of the production process. That is on the adjoining wing of the U-shaped facility. There, a top of the range Ringbuilder 3000 can be found. The Ringbuilder 3000 is a completely automatic combination of extruder and applicator and features a mobile touchscreen for the human-machine interface. The only actions that the operator needs to perform manually are loading and removing the casing and placing the rings on the divaricator fingers. The machine automatically recognises the casing so as to position the cushion gum and wingformer. The laser centring device ensures precise alignment and correct positioning of the ring on the casing (with the possibility of fine manual adjustment).
However, the newly-buffed casing has to get to the building process. Racking and monorails are normal and understandable solutions in most cases, but here at Alba Tyres they operate something that T&A has never seen at an independent retreader before – robotic transportation. This compact autonomous transporter takes each prepared casing to the next stage on behalf of operators. That reduces manual handling, contamination and frees technicians to focus on more complex and productive roles.
Throughout the process Alba Tyres reinforces its already intrinsically strong environmental credentials with the use of water-based adhesives. The particular products the Alba Tyres factory uses start off with a white gloss but dry clear.
Post-repair and rebuild the re-manufactured retreads are cured in the factory’s autoclaves at 115 degrees Celsius for the slightly longer than average time of 185 minutes. What follows is another highly automated process within the final inspection. Here a one-button operated machine pressure tests tyres for one minute each. Again, this provides the operator the necessary time and space to continue final inspection. According to those T&A spoke with, this TRM PTT 3000 automated pressure testing machine is the only one of its kind in the UK.
The overall impression is one of a modern factory efficiently producing high quality retreads. Look a little closer and there are repeated examples of how such quality standards bring with them a built-in sustainability emphasis too. Watching a robot deliver casings across the factory is always striking, but something that isn’t immediately obvious about that particular process is that not only is it autonomous, it can also be triggered and controlled remotely. Once again, this reduces the number of hands-on technicians required at any one moment, increases response time to any questions and really helps with things like lockdowns limiting the numbers of staff allowed on-site. It is also an indication of how the Alba Tyres’ retread operation has come a long way, but its development is still continuing.
Comments