Bandvulc’s investment in quality control and personnel development helps ‘set the standard for retreads’
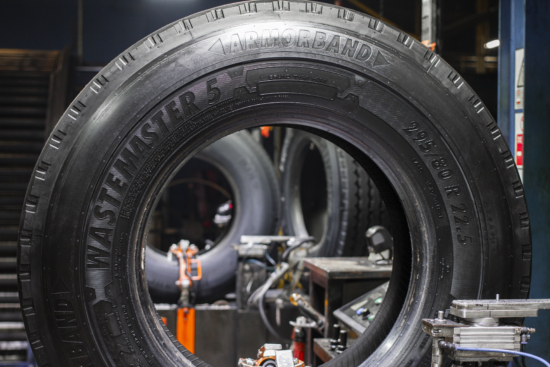
With more than 50 years of experience of retreading in the UK, Devon-based Bandvulc is well-known in the truck tyre and retread sectors. Over the years the company has established a reputation for producing top-quality retreads. Now, the Bandvulc says it is aiming to set the standard for retreading.
From the initial design and development work to casing recycling and tread application on the factory floor, Bandvulc implements measures designed to ensure its tyres perform across a range of applications. This is supported by the ongoing knowledge and expertise sharing partnership between Bandvulc and its parent company, Continental Tyres. Tony Mailling, Bandvulc Operations Director, explained the steps taken by the team at the Ivybridge factory to deliver the quality it does, beginning how they benchmark tyre quality:
“…First and foremost, Bandvulc tyres conform to the UN’s ECE Regulation 109, meaning that the performance, dimensions and tyre wall markings of Bandvulc products are similar to those of a brand new tyre.
Bandvulc puts casings through at least two shearography inspects, one at the screening stage and a second towards the end of manufacturing identify any weaknesses that may have developed during the tread application. (Photo: Continental)
“At Bandvulc, we audit our manufacturing process to the ISO 9001:2015 Standard. An ISO Standard ascertains quality and consistency by ensuring that a company is complying with its own standards time and time again. By implementing ISO, we can repeatedly deliver a high quality tyre that’s safe and reliable while also providing outstanding service to our customers. Legally, it also ensures that all the relevant documentation for Health and Safety, environmental impacts and quality control is in place.”
None of this would be possible without a highly skilled team in Ivybridge. To reach the strict requirements of the company’s ISO standards, Bandvulc representatives report that the company “invest significantly in training and personal development”. In fact, the most essential part of delivering a quality tyre is said to be a committed workforce.
One specific example of Bandvulc’s investment in continued professional development is its apprenticeship scheme. Though not currently recruiting for new starters, Bandvulc, has run a popular engineering apprenticeship scheme for several years. Trainees at the Ivybridge site learn a range of mechanical and electrical disciplines and can even get involved with Bandvulc’s cutting-edge robotics projects. After graduating from their apprenticeship, many team members continue their relationship with Bandvulc as permanent employees.
So, what steps are taken to ensure quality?
“Bandvulc’s retread tyre ranges use recycled tyre casings supplied by operators across the UK and the EU. Naturally, not every tyre will be up to scratch, depending on how it was used and maintained throughout its working life. We can inspect up to 2,500 casings a day. Around 30 per cent of the used tyres we review are unfit for retreading and are recycled”, Tony Mailling explained, adding:
“Evaluating a worn casing requires more than just a visual inspection, though we do review each tyre by hand. The casings are subjected to 20 different quality assurance checks and undergo a stage one shearography inspection. Shearography technology allows us to look through the core structure of the casing, identifying any issues or abnormal air pockets within the body that cannot be seen by a team member.
“Once we’re satisfied that the casing is fit for reuse, we constantly monitor its performance throughout the retreading process. We must spot a potential failure point at any stage – even after the
tyre production process has been completed and the tyre is prepared for shipping. One of the secondary inspection stages follows the removal of the existing tread from the casing, as that can reveal hidden internal damage.”After the retreading process is complete, technicians conduct a detailed pinhole test to locate any hairline breaches of the inner liner and inflate each tyre to 150psi to check tyre uniformity and structural integrity. Finally they run another shearography inspection to identify any weaknesses that may have developed during the tread application.
“It’s undoubtedly a belt and braces approach, but it’s nothing short of imperative that we’re confident in the quality, safety and reliability of every tyre leaving Ivybridge. By taking these necessary steps, we find that the claims on our tyres are just as low as they are for a range of brand new tyres”, Tony Mailling surmised.
But it doesn’t end there. Processes and procedures are constantly being reviewed:
“We’ve long held the belief that ‘standing still is going backwards’. In short, that means we’re always looking at ways to innovate and improve. Alongside our specialist team, technology plays a crucial role in meeting our ISO standards. Every Bandvulc tyre is barcoded and tracked throughout the production process. This means that we can identify the history of any tyre we’ve manufactured and can authenticate its quality post sale.”
All of the documentation for each tyre is accessible on a web-based system at every workstation. By taking this connected approach, the company can provide everyone with access to vital work instructions and technical information to certify consistent tyre quality. To that end, Bandvulc recently implemented a new app-based digital auditing system. Its deployment allows the team to use a simple app on a tablet as they go, cutting down on paperwork and increasing the efficiency of the process.
Comments