Vipal Rubber recognised for sustainable practices by EcoVadis
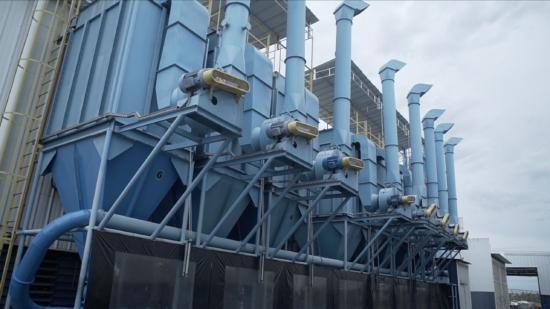
Vipal Rubber’s manufacturing units in southern Brazil have received recognition for sustainable practices. EcoVadis assessed the retreading materials supplier’s Nova Prata facilities, awarding it an additional two points versus its Silver-certificated inspection n 2019. Vipal said the sustainability of its operations, extending beyond the environment to focus on people too.
“We are totally focused on quality and on the continuous improvement of our industrial processes, human resources and commercial relationships with our suppliers and customers. Our objective is to continuously improve our practices and the management of socio-environmental initiatives, making our business even more sustainable”, says João Carlos Demoly, industrial director at Vipal Rubber. “The growth in our score demonstrates that we are on the right track, but that we still have room to evolve further. We are going to set new goals to continue improving our processes in all the aspects evaluated by the certification so that we can achieve an even better result in 2023.”
The EcoVadis assessment takes place every two years. In 2017, Vipal won the Bronze medal in its first participation. In 2019, the company achieved Silver certification by earning 59 points. In the assessment carried out in 2021, the achievement of 61 points demonstrated the evolution of socio-environmental processes and issues within the organization. EcoVadis’ assessment takes into account the following topics: Environment, Labor Practices and Human Rights, Ethics and Sustainable Procurement. The assessment methodology is based on international standards such as the Global Reporting Index (GRI), ISO 26000 and the principles of the Global Compact.
The EcoVadis rating is used as a benchmark by companies around the world for social and environmental practices. It is a solution used by multinationals to integrate CSR performance between buyers and suppliers. From the last result obtained, Vipal will establish evaluations and draw up an action plan to continue evolving in its sustainable practices.
Vipal’s socio-environmental actions
Tyre retreading, Vipal’s core business for 48 years, lends itself to sustainability. Brazilian Tyre Retreading Association (ABR) figures say each retreaded commercial tyre saves 50 litres of oil, versus the manufacture of a new tyre. It also estimates 26 million fewer tonnes of CO2 were emitted in 10 years due to tyre retreading. In the same period the ABR said the sector provided an oil economy in the order of 5 billion litres.
Vipal says its socio-environmental actions reach other areas of the company too. It started a programme in 2018 to develop sustainable practices. To implement the programme, the teams involved put 215 actions into place. Currently, the socio-environmental program is disseminated through sustainable procurement, environment, health and safety and human rights policies.
In Vipal’s Brazilian factories, a total of more than 30 million litres of effluents are treated per year. The use of water is another important point. At its factories in Feira de Santana (Bahia) and Nova Prata (Rio Grande do Sul), 92,000m² of roof is designed to capture rainwater, which is used for flushing toilets, production and irrigation. The plants have cisterns distributed throughout the industrial parks, with a storage volume of over 2 million litres. In addition, especially in Feira de Santana, part of the wastewater from reverse osmosis is used to flush toilets instead of using rainwater or drinking water for this purpose.
Vipal uses high technology to transform discarded rubber into powder through the cryogenic process, approximately 180,000 kg/month, which is recycled into other rubber products, such as flooring. The lighting of the factories is also obtained through the roofs with transparent acrylic coating installed in the factories, which result in a total of 171 thousand kWh/month of electric energy saved.
Vipal’s factories also have effective selective collection processes, achieving recycling rates above 80 per cent. In addition, it performs the reverse logistics of waste tyres in order to meet legal requirements and minimise environmental impacts via partner companies.
Comments