Welsh retreader Tuf Treads invests in Marangoni autoclave and nail hole detector technology
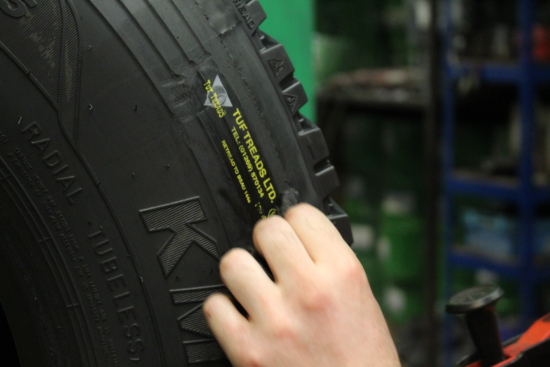
Llanelli-based Tuf Treads was founded in 1979 on a different location to where the retreading facility can now be found. Back then, current owner Mike Rees joined William Lloyd in the establishment of a new venture focusing on retreading tyres in four sizes according to the Peters system. Much more recently, the firm’s current Cross Hands retreading factory took delivery of a new Marangoni nail-hole detector to upgrade its quality control procedure, something that is just the latest in a history of steady development at the company. Tyres & Accessories visited Tuf Treads to find out more about the company’s past, present and future.
Steady growth over four decades
As we have seen, initially, Tuf Treads started out retreading four sizes back in 1979 with the Peters System. However, it wasn’t long before the company embarked on what turned out to be a four-decade long relationship with Marangoni. This began in 1983 when Tuf Treads invested in the Ringtread system, before expanding it options again in 1985 to include as many as 50-60 sizes.
The changes in production system as well as investments in retreading equipment meant the capacity of the operation grew significantly from its initial levels of roughly 40 units a week in 1979. Key investments included the purchase of a second autoclave in 1984, followed by a third in the early 1990s. Of course, since autoclaves accounting for a key bottleneck in production, Tuf Treads’ investment in additional autoclaves has had a marked impact on production capacity. Those investments mean the Cross Hands site has been able to increase capacity to around 50 units a day since the 1990s and onto today’s current levels.
As far as sales are concerned Tuf Treads’ retreads are sold direct to users, with the company’s customer base largely comprised of local hauliers. In addition, the company is involved in some pockets of low-level wholesale business in partnership with some local tyre distributors. And, as you might imagine with a business of this sort, the company also sells new tyres. Indeed, this – along with the management humble but steady growth philosophy – demonstrates that the business knows its own mind when it comes to products, customers and indeed pricing. As far as the latter is concerned, this means that the company won’t be drawn into a race to the bottom.
Investing in the production line
Tuf Treads invested in the Ringtread system in 1983, the technology may have been upgraded – nowadays Tuf Treads process centres on machinery such as the Marangoni’s Ringtreader 200 – but the emphasis on Ringtread remains (Photo: Tyre Industry Publications Ltd)
The latest addition to Tuf Treads’ production line is a Marangoni nail hole detector, which was purchased in 2020, but – due to coronavirus restrictions – its installation wasn’t completed until the first quarter of 2021. Now, however, the nail hole detector is fully employed, being utilised as it is on every single tyre that is retreaded in Cross Hands.
Once casings are acquired by Tuf Treads, having been sourced from end-user customers with a few more being sourced from casing dealers, they are all run through the nail hole detector. Not only does this identify metallic foreign objects, but it also helps highlight other potentially underlying structural problems with incoming casings. For the same reason, tyres are then “nail-checked” a second time at the end of the process in order to weed out any potential problems before they happen.
The company normally only accepts premium casings and actively rejects Chinese-manufactured casing on the basis that most are incompatible and/or problematic when it comes to retreading.
On the subject of quality control, each tyre that rolls off the production line bears the Tuf Treads logo, while also testifying to the fact that all tyres are retreaded according to the BSAU 144e standard. The date marks of casings are also all checked at the initial inspection. During the retreading process, date codes are added on both sidewalls, something that helps DVSA inspectors – especially in the case of twin fitments.
During the buffing phase of the process, Tuf Treads positions its buffers over a pit with built-in extractors all around. This produces both a better working environment for the buffing technician and an overall cleaner working area that results in factory efficiencies as a consequence of reduced cleaning.
Once inspection and buffing are complete, the appropriate and necessary repairs are made and new treads are applied. As we have seen, Tuf Treads are a loyal Ringtread customer and somewhere between 95 and 98 per cent of output is Ringtread based. Tuf Treads’ Ringtreads are manufactured using Marangoni’s range of compounds, which specifically includes premium Black Line-branded compounds.
With new treads applied, tyres are put in envelopes (supplied by MaE) and arranged ready to be transported into the autoclave for curing. Tuf Tread utilises modern Marangoni (TRM) autoclave technology for the bulk of its retreading, but the company kept one of its old autoclaves to facilitate occasional short run retreads and major repairs.
Resilient throughout 2020
Whatever else happened during the last year or so, Tuf Treads’ business proved to be as resilient as its retreaded tyres in the fact of the pandemic and the lockdowns that came with it. During the first lockdown, Tuf Treads took the difficult decision to furlough for a couple of weeks. However, the almost immediate feedback was that demand was up not down.
In light of increased rather than decreased demand from Tuf Treads’ independent haulier customer base, the relatively new addition of the Marangoni (TRM) autoclave turned out be great news. Following a smooth installation, this particular piece of kit helped the business catch up from the preceding weeks of lockdown and overtake pre-lockdown levels in two-to-three months.
All-in-all, steady growth over four decades supported by treads and machinery from Marangoni appears to be a winning combination for Tuf Treads – the Welsh-based retreader that is set to continue quietly getting on with business into the next generation.
Demand for Tuf Tread retreads help up and even expanded during the lockdowns of 2020 (Photo: Tyre Industry Publications Ltd)
Comments