Magowan’s pioneering paperless warehousing in the tyre business with Cam systems
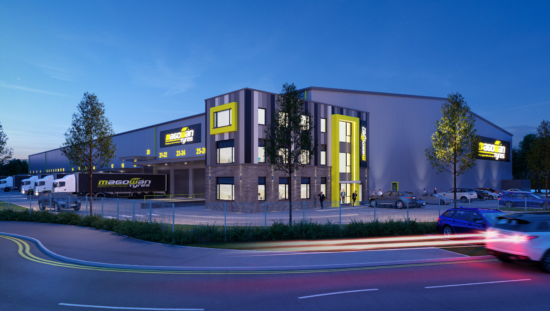
Magowan’s new warehouse currently occupies a 120,000 square foot footprint within a 15-acre site plot. Of this, 100,000 is pure warehousing with the remaining 20,000 square feet housing modern offices. While there is plenty of room in the current structure and – as we will see – significant efficiencies. There is both the space and the will to further expand capacity, with an additional storage building next to the faster-moving connected logistics hub.
Eight “goods in” doors lead to loading and unloading inter-roll belts that make manual handling as safe and efficient as possible for the team. As a result, they can load three trailers at once (if needed) and can load with a minimum of two people – one picking onto the belt and another lacing into containers. Previously this process alone took almost twice as much manpower (three to four people).
A blank canvas project
Tyres, stillages and vans are all identifiable and locatable via Cam’s WMS software (Photo: Chris Anthony, Tyre Industry Publications Ltd)
The project was a real blank canvas endeavour, with Magowan’s senior executives thoroughly considering the logistics, financial and overall business case for its clean-slate approach. This meant that the business could literally build in processes that it had never implemented before. For example, RFID chips mounted in the concrete floor help the automated systems find where they are up and down aisles that are also wire guided. On-board computers mean equipment is constantly in-touch with the wider system and with the stock staff, supervisors and managers.
But nothing happens by accident and the radical overhaul of operations at Magowan’s is now different. Of course, there is the £10.5 million overall investment figure, but sometimes the impact associated with understanding what’s involved can be lost in multi-million-pound sums. With that in mind, here’s a more concrete example – in order to properly utilise the site, specialist forklift pickers have been purchased. They cost £80,000 each and Magowans have several on the go.
Since the intelligent system knows the intimate details of each tyre logged in the software – including its DOT code – the Magowan’s team are able to ensure that the warehouse works to first-in first-out principles and that stock is kept as “fresh” as possible. But knowing such details also brings other strategic benefits. For example, should a manufacturer recall a certain make and model, identifying which tyres need to go back to the factory is far easier than it ever was before.
The Covid-19 pandemic as well as its inherent lockdowns came right in the middle of the Magowan’s project. Once the dust settled, owing to the many efficiency increases that come with the warehouse and its systems, it soon became apparent that previous staff levels were no-longer necessary. Indeed, the combination of disruptions led to a new normal with a 20 per cent reduction in headcount that means not just fewer staff, but also the most experienced and efficient staff remain.
The impact on the working week provides another illustration of increased efficiencies. Before the warehouse(s) ran from 6:30 to 17:30 Monday to Friday, with occasional weekend work on top of this. Now the new warehouse runs 8:00 to 17:00, five days a week. It is worth pointing out that Magowan’s old hours, while much longer than the post-investment levels, are actually still shorter than other comparable tyre wholesale businesses, some of which run 24-hours a day. But in any case, the advantages are clear.
With this in mind, it is easy to see how the work done so far is said to have “improved the business immeasurably”. There are “fewer mistakes”, with day-to-day operations running “more efficiently”. The fact that considerably fewer credit notes are issued for the accidental mis-picking of slightly incorrect tyres (such as 205/55 R16 V instead of a 205/55 R16 W, for example) further exemplifies the point.
From a logistics perspective, moving to Cam’s WMS as part of the overall project creates more time and space for planning. For example, in the export aisle tyres can be picked for loading a week ahead of time so they are ready for the driver to deliver to the port or final destination.
All this was achieved through the connected identification of tyres, aisles, racking and the stillages themselves. As well as the in-built RFID chips found in the floor, each stillage is also equipped with both RFID and barcode identification, which means warehouse operators (and the system itself) have immediate access to the content of any stillage in any location at the touch of a button via a tablet device. Supervisors too, can locate any tyre or stillage anyway in the warehouse via a click of the mouse with the CAM WMS system.
Significant technology upgrades can be found at the loading stage too. As well as the manual handling benefits of the inter-roll belts installed at the loading doors, the belts also offer further quality control opportunities. First of all, infra-red sensors are positioned at the loading end of each belt to precisely count each order and present the results with large LED screens. This way, the company and its customers can have confidence that they do receive exactly what they pay for. In addition, the belts are also fitted with high-definition video cameras which record the loading process and offer footage sharp enough to read the sidewalls of the tyres loaded. Should questions be asked, this footage can then be interrogated in order to find out exactly what happened with each order.
There’s no doubt that going paperless is a big step – both in terms of complexity and investment. But, if you are prepared to invest in the infrastructure, systems and – just as importantly – the new ways of thinking, working and training, the benefits are huge. Put that all together with the fact that there’s not an independent tyre wholesale warehouse like it in the country and it is fair to say that the Magaowan’s project is pioneering as well.
Darryl Magowan Snr., Darryl Magowan Jnr (pictured) as well as David Magowan and IT manager Ben Tinsley showed T&A around (Photo: Chris Anthony, Tyre Industry Publications Ltd)
Comments