Bentley & Bucci develop 22” carbon fibre wheel
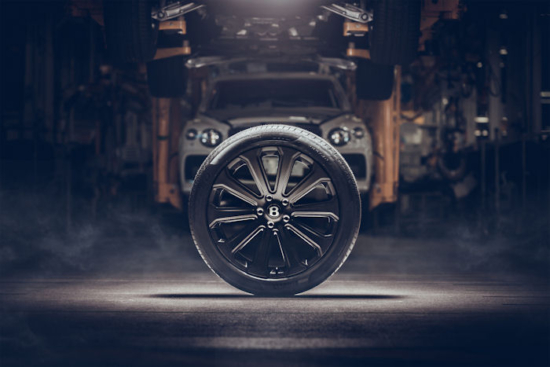
As Jeremy Clarkson may have uttered back in the pre-Steakrage glory days of Top Gear, this is the biggest carbon fibre wheel…in the world. After years of development with one of the world’s leading composite suppliers, Bentley has unveiled a new carbon fibre wheel developed specifically for the Bentayga. The 22-inch carbon wheel, engineered with renowned specialists Bucci Composites, is to be the largest carbon wheel in production globally and offers a vast range of benefits beyond the initial 6-kilogramme improvement in unsprung mass per wheel.
The new carbon wheel has been subjected to exceptionally rigorous TÜV standards and is the first carbon wheel ever produced to pass all tests. The newly-developed rim has undergone the most rigorous testing for non-metallic wheels according to the new TÜV standards including biaxial stress testing, radial and lateral impact testing for simulating potholes and cobblestones, tyre overpressure, and excessive torque tests exceeding the permitted limits.
One of the most severe tests of the TÜV requirements – the impact test – has shown how the carbon rim is extremely safe in addition to the performance benefits. After a severe impact which would crack or shatter an aluminium wheel, causing the tyre to collapse explosively, the carbon fibre rim allows a slow tyre deflation thanks to the intelligent layering of fibre weaves, allowing the vehicle to come to a controlled, safe stop.
For the final sign off stage, the wheel was put through its paces on one of the most famous tracks in the world – the Nürburgring Nordschleife.
Technological benefits of composite wheels
Carbon fibre not only provides a significant weight saving, but also offers the additional benefits of increased strength and stiffness. This leads to a number of fundamental benefits:
Increased safety – when the rim receives a high impact, the weave pulls apart leaving openings to allow gradual air loss rather than instant deflation like an aluminium rim.
Increased steering agility – the 6-kilogramme weight saving and the high stiffness afforded by the properties of carbon fibre mean a more stable and consistent steering platform. In comparison, a forged aluminium rim can lose up to a degree of camber due to wheel flex, reducing grip and agility.
Improved and more responsive braking thanks to the decrease in unsprung mass.
Reduced tyre wear – Since the stiffer carbon rim does not suffer from the same amount of bending, it allows for greater tyre stability and a more consistent contact patch thanks to a larger tyre support surface.
Innovative production processes
One of the main innovations lies in the rim manufacturing process, which involves the application of innovative concepts (covered by patents) combined with the use of high-pressure resin transfer moulding (RTM). The materials and production parameters have been carefully studied to ensure the repeatability of the product without affecting its quality.
The process involves the cutting of carbon fibre cloth into prescribed shapes. The weave segments are then stacked, heated and draped into a mould to create three-dimensional preforms. The preforms are collated and arranged into a larger mould before resin and hardner is injected throughout. After curing time at temperature, the component assembly is removed from the mould, and the final surfaces are machined to the correct finish, before polishing.
The new wheel will be available to order late 2021.
Comments