Bridgestone: Looks are deceptive when it comes to agricultural tyres
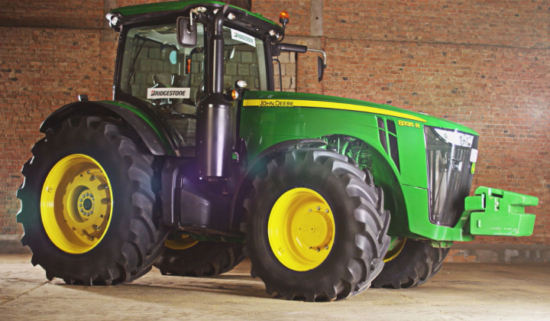
Agricultural tyres generally appear quite similar irrespective of brand, making it difficult to spot at a glance the difference between discount tyres and higher-priced premium products. Bridgestone observes that price thus “wrongly becomes a differentiating element” with these products. The tyre maker is concerned that some may gain the impression they’re paying extra for the brand rather than the tyre, and wishes to set the record straight.
Not only do the manufacturing processes used result in a “huge difference” to the final product, Bridgestone says the basic materials that go into the tyre “change everything.” They give it better wear properties, greater resistance to cuts and perforations, more suppleness, higher driving comfort and stability, better soil preservation and safer on-road driving.
“In short, even if they look alike on the outside, top-of-the-range tyres are the fruit of the complex blending of very specific high-quality materials which offer you a maximum lifespan and optimal productivity,” comments Bridgestone.
The tyre maker stresses that a top-of-the-range tyre is the “result of mixing very specific doses of raw materials.” It has compiled a list of the “essential materials” – the rubbers and additives – that make a difference in its agricultural tyres.
Rubbers
Natural rubber: This is one of the basic components of tyre rubber, with irreplaceable elasticity, resistance, adherence and impermeability characteristics. It comes from Hevea tree sap, in the form of a white liquid which is then coagulated to obtain natural rubber. This substance is perfectly suited to the vulcanisation process which transforms it from plastic to elastic.
The proportional share of this basic ingredient makes the first difference between a good quality and a low quality tyre. Discount tyres are essentially made up of much cheaper synthetic rubber, which is less durable and not recyclable.
The Bridgestone group uses sustainably managed natural resources and possesses its own Hevea tree plantations in Liberia. This ecological management of resources allows the group to balance out its supplies with a long-term environmental vision, with the aim of achieving a 100 per cent sustainable use of materials in the coming years.
Synthetic Rubber: Derived from hydrocarbons, synthetic rubber is mixed with the natural rubber to improve resistance. Styrene-butadiene is used in the tread to increase resistance to abrasion and reduce ozone sensitivity. Butadiene is used in the sidewalls to increase resistance to impacts.
Image: Bridgestone
Additives
These improve the basic rubber mixture and are essential to obtain a high-quality tyre. Bridgestone comments that manufacturers of discount tyres often make savings on these products.
Processing additives: These additives – resin, oil and bonding agents – are used to obtain a perfectly uniform and supple mixture which helps to reduce the cost of moulding. The resin acts as an anti-fixing agent which facilitates the work of the crude rubber during blending, extrusion and calendering. The oil plays a softening role, softening the crude rubber and facilitating the blending process. The bonding agent ensures the cohesion of the mixture which is carried out by mechanical blending.
Image: Bridgestone
Additives to improve the tyre: These – additives – protective agents and carbon black – improve the quality of the tyre, its resistance and its lifespan. Derived from the combustion of hydrocarbons, carbon black this is a very important material for the tyre. It makes up about 30 per cent of its composition and is responsible for the black colour common to all tyres since the early decades of last century. Carbon black increases the rubber’s mechanical resistance and allows for more even heat distribution. It can also reduce tyre deflection, thus optimising rolling resistance.
Protection agents are antioxidants that protect the rubber from oxidation by the ozone or oxygen in the air and thus prevent the sidewalls becoming cracked over time or prolonged exposure to the sun.
Image: Bridgestone
Additives for vulcanisation: Vulcanisation brings about changes to molecular chains in the rubber, and this curing stage is aided by zinc oxide, sulphur and vulcanisation accelerator. The first of these, a mixture of oxygen and zinc, enables the tyre to resist rising temperatures and facilitates the vulcanisation process. The third is, as its name suggests, an agent that accelerates the vulcanisation process.
As for sulphur, it is one of the main vulcanising agents. It increases mechanical resistance and ensures the rubber’s elasticity while reducing sensitivity to variations in temperature. It is a central element in molecular bridging – too much sulphur and the tyre will be too rigid, not enough and the molecule cohesion will be insufficient, making the tyre not very resistant to wear.
Image: Bridgestone
Material assembly
In addition to the raw materials themselves, the process by which these materials are brought together is also instrumental in giving a tyre its characteristics. Bridgestone states that the processes it employs derive from “thousands of hours of tests and research and development” and result in “a top-range tyre with exceptional characteristics.”
One of the essential components of tyre resistance is the inclusion of either fabric or metal fibres within the rubber.
Maximum resistance can be obtained by using metal mesh, which provide excellent resistance to impacts, punctures and flexion. These metal cables made up of twisted wires that are a mixture of steel, copper and zinc, and are highly rigid. While this rigidity is particularly suitable for heavy machinery or specialised tyres, it is less suitable for field crop or polyculture applications, where soil preservation is crucial. Nylon, polyester or rayon fibre mesh is used here instead.
This fabric mesh offers a major advantage in terms of elongation and reinforces the tyre’s structure while retaining its suppleness and ability to work at very low pressure. These layers of fabric are processed in a latex bath for perfect adhesion with the surrounding rubber.
A top-quality tyre is a complex unit that takes into account the interactions of each of its components. For example, the rubber used for the interior of the tyre must have superior hermetic characteristics in order to contain pressure, the sidewall rubber must provide maximum suppleness but resist impacts, while the tread rubber must be ultra-resistant to wear but very stable to transmit tractive force and engine torque to the ground.
Image: Bridgestone
An agricultural tyre is made of the following components:
Casing or inner liner: This internal tyre material must keep the air in, resist loads and absorb shocks. It contains a large portion of totally hermetic synthetic rubber, such as Isobutylene Isoprene.
Sidewalls: Good quality sidewalls offer maximum suppleness while preserving lateral stability. They absorb shocks and ensure protection against external cuts.
Plies or mesh: These are different overlapping layers of fibres and rubber which make the tyre resistant to impacts. The first plies ensure protection, then come the stabilising plies. They allow the full width of the tyre to be used and perfect command of steering. Bridgestone comments that some manufacturers keep the cost of their agricultural tyres down by reducing the number of plies to a minimum.
Tread: Bridgestone calls this the “most complex assembly.” The tread contains the rubber that comes in contract with the ground as well as many stabilising plies on top of the plies that protect the casing. The manufacturer points out that the tyre’s lifespan as well as its resistance to cuts and external damage depends on the quality of the tread. The final profile of the tread is obtained using the mould cavity during vulcanisation, and the stability of the tractor when driving and during steering manoeuvres depends on the quality of this profile.
Beads: These are extremely resistant metal wires located on the inside of the tyre bead. They are essentially made of steel that is mixed with copper and tin to ensure adhesion with the rubber. The beads make it possible to maintain the casing ply turn-ups and reinforce the rigidity of the bead. This ensures the liaison between tyre and rim seat and enables the transmission of engine power.
Image: Bridgestone
Advantages of a top-quality tyre
“Like in all sectors of activity, top quality equipment cannot be judged only based on its external appearance,” reiterates Bridgestone. “Your tractor’s engine power may be very different, even if the external bodywork is similar. The same applies for the quality of tyres, but with extreme differences between tyre ranges, because unfortunately you cannot see inside the rubber unless you cut it. What is visible, on the other hand, is the performance, for which there is no comparison possible between standard tyres and top-quality tyres.”
Bridgestone emphasises that high-tech tyres such as its VT-Tractor offer a number of advantages in regards to load, soil preservation, traction, working time, lifespan and on-road use.
Comments