Michelin validates Carbios plastic bottle to tyre recycling technology
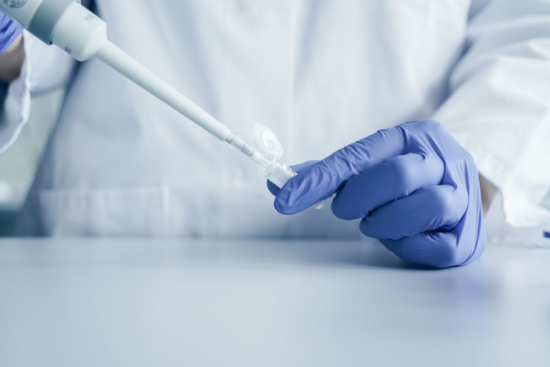
Every year, 1.6 billion car tyres are sold worldwide in total. The PET fibres used in these tyres represent 800,000 tonnes of PET per year. With regards to Michelin alone, this represents nearly 3 billion plastic bottles annually. That’s why the France-based global tyre maker has been looking for ways that bottles can be recycled into technical fibres for use in the company’s tyres. Now, the company has validated that Carbios’s enzymatic process does exactly that, giving Michelin a step forward in its sustainability plans. Indeed, Michelin describes the development as “a major step towards developing 100 per cent sustainable tyres. Michelin has successfully tested and applied”. Michelin is committed to achieving 40 per cent sustainable materials (of renewable or recycled origin) by 2030 and 100 per cent by 2050.
“We are very proud to be the first to have produced and tested recycled technical fibres for tyres. These reinforcements were made from coloured bottles and recycled using the enzymatic technology of our partner, Carbios,” said Nicolas Seeboth, Director of Polymer Research at Michelin. “These high-tech reinforcements have demonstrated their ability to provide performance identical to those from the oil industry.”
Conventional thermomechanical recycling processes for complex plastics do not achieve the PET high-performance grade required for pneumatic applications. However, the monomers resulting from Carbios’ process, which used coloured and opaque plastic waste such as bottles, once repolymerized in PET, made it possible to obtain a high tenacity fibre meeting Michelin’s tyre requirements.
According to Michelin and Carbios, the technical fibre obtained is of the same quality as the one from virgin PET, processed with the same prototype installations. This high tenacity polyester is particularly suitable for tyres, due to its breakage resistance, toughness, and thermal stability.
Carbios’ enzymatic recycling process uses an enzyme capable of depolymerizing the PET contained in various plastics or textiles (bottles, trays, polyester clothing, etc.). This innovation allows apparently infinite recycling of all types of PET waste. It also allows the production of 100 per cent recycled and 100 per cent recyclable PET products, with the same quality as if they were produced with virgin PET.
“In 2019, Carbios announced it had produced the first PET bottles with 100 per cent Purified Terephthalic Acid (rPTA), made from the enzymatic recycling of post-consumer PET waste. Today, with Michelin, we are demonstrating the full extent of our process by obtaining from this same plastic waste, recycled PET that is suitable for highly technical fibres, such as those used in Michelin’s tyres,” said Alain Marty, Carbios’ Chief Scientific Officer.
At the end of September 2020, Carbios announced that it had planned for all its teams and facilities to be based on a single site belonging to the Michelin Group by 2022. The facilities made available to Carbios will specifically be in Clermont-Ferrand and willl accommodate all the company’s activities which are currently spread over several locations. In particular, they will include the development laboratory, the pilot facility and demonstration plant of Carbios’ enzymatic recycling technology for PET plastics and fibres.
Comments