Cooking up better tyre pyrolysis oil compounds
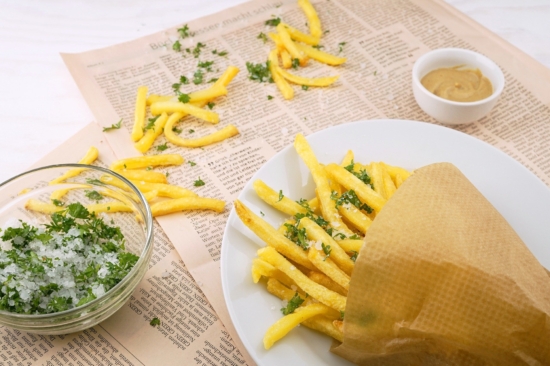
“Wastes to energy: Improving the poor properties of waste tire pyrolysis oil with waste cooking oil methyl ester and waste fusel alcohol – A detailed assessment on the combustion, emission, and performance characteristics of a CI engine”, published in the journal Energy on 22 January 2021; and “Thermodynamic comparison of pyrolysis and gasification of waste tyres”, which was published in the Journal of Environment Chemical Engineering on 30 January 2021 complete our recent review of the latest peer-reviewed pyrolysis research.
Continuing the theme of how to best utilise the material outputs of tyre pyrolysis, “Wastes to energy: Improving the poor properties of waste tyre pyrolysis oil with waste cooking oil methyl ester and waste fusel alcohol – A detailed assessment on the combustion, emission, and performance characteristics of a CI engine” was written by Ümit Agbulut and Suat Sarıdemir from Department of Mechanical Engineering, Düzce University and Murat Kadir Yesilyurt from the Department of Mechanical Engineering at Yozgat Bozok University. The three Turkish researchers’ paper set out to improve the performance of waste tyre-derived pyrolysis oil/diesel fuel blends. Specifically, they sought to achieve this by reducing “the worsened combustion, emission, and performance characteristics of a CI engine fuelled” by tyre-derived oil/diesel.
In order to achieve their goal, the researchers compared four fuels: 1) 100% diesel fuel; 2) 20% waste tyre pyrolysis oil/80% diesel fuel; 3) 10% pyrolysis oil and 80% diesel fuel containing 10% waste biodiesel; and finally 4) 10% waste tyre pyrolysis oil and 80% diesel fuel containing 10% waste fuel oil. The tests were performed at a constant engine speed of 2400 rpm, and varying engine loads.
As a result, the researchers found that the waste tyre pyrolysis oil/diesel fuel blend reduces thermal efficiency by 9.13 per cent. However, this figure was improved by 7.51 per cent and 3.82 per cent respectively with the addition of waste biodiesel and fusel (alcohol oils) respectively.
On the other hand, the researchers also found that the waste tyre pyrolysis oil/diesel fuel blend increased specific fuel consumption by 21.78 per cent. However, this increase was pulled back by 8.89 per cent and 12.57 per cent for waste biodiesel and fusel oil respectively. As a consequence, the research concluded that waste biofuels including waste cooking oil can “improve poor combustion, emission, and performance characteristics of binary waste tyre pyrolysis oil diesel blend”.
Therefore, the scientists suggest that mixing waste biofuels into tyre pyrolysis/diesel fuels rather than waste tyre pyrolysis oil alone. In other words, cooking up a mixture of tyre-derived oil/diesel and something like chip-fat is one of the best ways to improve the fuel’s performance characteristics. The scientists also suggested future research into the addition of “metal oxide-based nanoparticles”. However, this comes at a financial cost to the industrial process. And so, the researchers also suggested the “re-evaluation of waste products for beneficial forms” could be “motivated by government incentives” allowing “researchers to focus on how the cost can be reduced in future works.”
Turn or burn – pyrolysis and gasification compared
The latest piece of research, “Thermodynamic comparison of pyrolysis and gasification of waste tyres”, was produced by Athi-enkosi Mavukwana, Stacey Neil, James Alistair Fox and Baraka Celestin Sempuga from the Department of Civil and Chemical Engineering, College of Science Engineering and Technology, University of South Africa (UNISA); Institute for the Development of Energy for African Sustainability, College of Science Engineering and Technology, University of South Africa (UNISA); and School of Chemical & Metallurgical Engineering, University of the Witwatersrand between them.
The researchers analysed a range of pyrolysis and gasification pathways in terms of the fundamental thermodynamic metrics of carbon efficiency, atom economy, efactor and chemical potential efficiency and also their market-related revenue potential. Specifically, they used “a fundamental thermodynamic analysis” to compare two technologies of converting waste tyres to useful products. The comparison was based on “carbon efficiency and exergy efficiency or chemical potential efficiency”. In other words, it looked at “how much of the carbon in the tyre is transferred to the useful products and how much of the energy content in the tyre has been transferred to the product which indicates the potential impact to the environment of each process”.
In conclusion, the researchers found that both gasification and pyrolysis are “viable for eliminating” and “converting” tyre waste into “useful products”. Thermodynamically, the pyrolysis process performed better than the gasification route, with a higher overall carbon efficiency and chemical potential efficiency. Or, to put it another way, pyrolysis “conserves the carbon resource and has minimal impact to the environment”.
Indeed, the gasification route loses about 45 per cent of the carbon feed to carbon dioxide. Therefore, a carbon capture system is needed in order to make the processes more environmentally friendly. However, this further increases the capital cost of gasification projects.
Pyrolysis, on the other hand, is simpler to build and operate. But the pyrolysis route has drawbacks when it comes to product quality (compared to commercially available transportation fuel and carbon black products). Furthermore, “substantial refining is required for all the pyrolysis products, whereas the gasification route produces products that meet the requirements from the start”.
Gasification also offers more obviously immediate financial returns: “The gasification route offers the highest revenue per ton of waste tyres at $625 per ton of waste tyre compared to $205 per ton achievable by the pyrolysis process. Of course, such a difference is difficult to reconcile even though pyrolysis offers “better environmental performance”. Unless the technology can be integrated in a wider sustainable product cycle, that is.
According to the researchers, “commercial pyrolysis processes will always suffer from financial difficulties due to the fact that off-take agreements are difficult to secure.” However, when you consider that most of the recent pyrolysis investments are in connection with either tyre or petrochemical companies you see another reason why interest in pyrolysis has spiked.
The paper’s conclusion that “from an environmental standpoint, converting waste tyres to transportation fuels is preferable to landfill” is a remarkable vote of confidence in pyrolysis even if it is tempered by qualifications that gasification is simple and more profitable without vertical integration. However with fossil fuels being consumed and burned all over the world, recycling and even re-using waste tyres in either of these ways is much better that failing to capitalise on their benefits.
Taken together the three papers are emblematic of recent developments in the tyre pyrolysis sector and go a long way towards explaining why interest in the technology has peaked in recent months. The peak in interest can be boiled down to the following four reasons: Because pyrolysis technology has come on in leaps and bounds in general – both in terms of effectiveness and simplicity; because new techniques are increasing the efficiency of reclaiming raw materials such as carbon black all the time, as “A novel approach of reapplication of carbon black recovered from waste tyre pyrolysis to rubber composites” demonstrates; because the performance characteristics of reclaimed materials can be further improved by combining them with other sustainably-sourced recycled materials (see “Wastes to energy: Improving the poor properties of waste tyre pyrolysis oil with waste cooking oil…”); and because tyre pyrolysis can offer incomes of $205 per ton exclusive of any of the vertical integration benefits that most of the petrochemical and tyre manufacturing related projects will achieve.
Comments