Spike in tyre pyrolysis investment backed by flurry of related scientific research
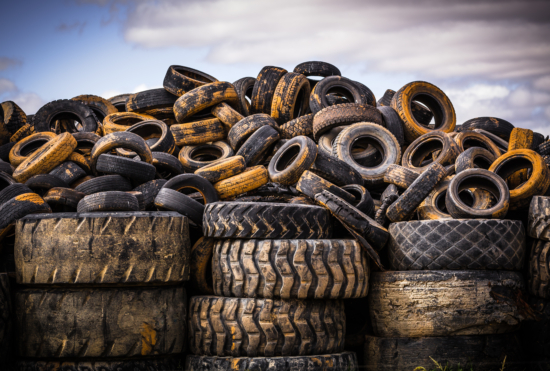
We have all witnessed the recent spike in interest in tyre pyrolysis-related recycling during the last year or so. The concepts themselves are not new, so what is behind renewed interest and confidence in such projects? As well as an uptick in investment in tyre pyrolysis plants, the last few months have also seen the publication of a flurry of peer-reviewed research papers into different aspects of waste tyre pyrolysis. As part of this year’s annual Tyre Recycling feature, we took a look at the three most recent papers in order to find out more.
Specifically, we reviewed “A novel approach of reapplication of carbon black recovered from waste tyre pyrolysis to rubber composites”, published online in the Journal of Cleaner Production on 1 October 2020; “Wastes to energy: Improving the poor properties of waste tire pyrolysis oil with waste cooking oil methyl ester and waste fusel alcohol – A detailed assessment on the combustion, emission, and performance characteristics of a CI engine”, published in the journal Energy on 22 January 2021; and “Thermodynamic comparison of pyrolysis and gasification of waste tyres”, which was published in the Journal of Environment Chemical Engineering on 30 January 2021.
A new approach recovering carbon black from tyres
“A novel approach of reapplication of carbon black recovered from waste tyre pyrolysis to rubber composites” is the culmination of cross-departmental research conducted by Xiaolong Tian Qianxiao Zhuang, Shuang Han, Shaoming Li, Haichao Liu, Lin Li, Jinxiu Zhang, Chuansheng Wang and Huiguang Bian within three different laboratories in Qingdao, Shandong Province, China, namely: National Engineering Laboratory of Advanced Tire Equipment and Key Materials, Shandong Key Laboratory of Advanced Manufacturing of Polymer Materials, and the School of Mechatronics Engineering.
Noting that pyrolysis carbon black (CBp) accounts for about 35 per cent of the resultant material output of tyre pyrolysis, the researchers highlighted that CBp represents “one of the bottlenecks in the waste tyre pyrolysis industry”. The reason? Generally, the properties of CBp/rubber composites aren’t of a high enough standard for use in tyres because of their “poor reinforcement and dispersion”. And that’s where’s the Chinese researchers’ “novel approach” known as the “atomization dispersion and high temperature sputtering drying” method comes in.
Ultimately, the paper concludes that the performance characteristics of CBp/rubber composites prepared via the ADSD method was better than that those produced with the traditional method. Indeed, CBp/rubber composites made by the ADSD method were said to be superior “in terms of vulcanization performance, physical and mechanical performance” and “dynamic performance”.
The conclusion of the paper also carries within it the implicit warning that, while the pyrolysis of waste tyres would generate a large amount of CBp, CBp made by some conventional methods “has many impurities and low activity, making it difficult to re-use”. As a consequence of this “secondary pollution to the environment” and “failure to achieve the purpose of recycling waste tyres” are real risks.
Therefore, the research suggests “re-applying the CBp to manufacture tyres through activation and appropriate processing technology is the best scheme to realize its high value utilization.” Furthermore, the ADSD mixing method is reported to realize “uniform dispersion and instantaneous drying of the CBp in the latex by high pressure gas and high temperature, and the performance of CBp/ rubber composite by ADSD method” and is described as “better”.
Comments