Vipal evaluating use of rice husk in its compounds
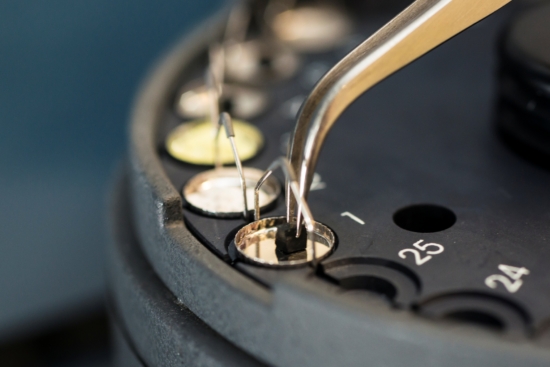
Vipal Rubber is researching the possibility of using rice husk residue as a raw material for the rubber industry, the result of a partnership between Vipal, the University of Caxias do Sul, in Brazil, and Lodz Poland University of Technology. Goodyear released a rice husk silica tyre in China in mid-2015, before announcing in November 2020 that it would double its rice husk usage by 2021; and Pirelli announced that it was researching the use of rice husk ash in new tyre compounds back in April 2009; but Vipal is the first retreading compound maker to go public with its use of rice husks in compounding.
One of the participants in this initiative is the Material and Chemistry Engineer, Suélen Moresco, from Vipal’s Research team, who recently won an Industry Researcher award due to the set of studies focused, for example, on the development of sustainable technological products and processes. Suélen points out that the remainder of the rice production is used as fuel for thermoelectric power plants and from this energy generation there is still the ashes from the burning of the residue, object of study of the Vipal project, which foresees the treatment of this by-product.
The research is still at the stage of internal laboratory validation and should go on to tests at the factory. The patent application for the process has already been filed by Vipal and the participating universities. According to the researcher, in addition to providing an appropriate destination for the waste, one of the advantages of using rice husk ash, is to diversify the raw materials within the rubber chain.
The project aligns to Vipal with the 2030 Agenda, a series of commitments instituted by the United Nations. It also aligns with Vipal’s plans to participate in the circular economy, something the company is already doing with its ECO Treads products, which are designed to generate less fuel consumption from vehicles due to their rubber compound.
According to Rodemir Conte, Product and Process Engineering Manager at Vipal Rubber, the development of these new products is a long-term job: “Vipal invests a lot in research and this keeps it strong and in constant renovation. These products put the company one step ahead of the competition in a market that needs this renovation and alternatives that reduce environmental impacts”.
For Frederico Schmidt, general manager of Vipal in Europe, the concept of sustainability combined with innovation and technology is a differential of the company. “Important markets for the brand are increasingly adopting measures that take into account the Circular Economy, such as Spain, France, Germany and other countries. In this way, Vipal is at the forefront, whether through research, products or solutions that meet the most diverse socio-environmental aspects of the transport sector and industry as a whole”.
Vipal has three distribution centres in Europe – Valencia (Spain), Felixstowe (UK), and Nova Gorica (Slovenia) – to meet the growth in exports to the European market. Following this strategy, the company also dedicates one of its four plants exclusively for exports.
Comments