NeroForce introduces two new buffing technologies
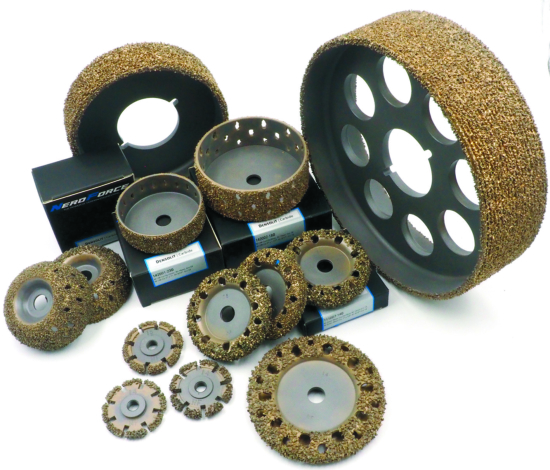
NeroForce is introducing two new technologies that help improve buffing tasks during retread production – Densolit Carbides and X-technology for unit wheels.
Firstly, Neroforce is expanding its line-up of carbide retreading tools with the addition of Densolit Carbides, which the company says are “revolutionary”. Densolit Carbides are exposed to a new treatment in which a fine bionic sealing layer is applied to the abrasives. Why is this coating technology so pioneering? With all carbide tools, the base body is coated with carbide split and then traditionally coated with paint (copper, gold or silver). This coating protects against rust and improves the appearance. However, due to the thickness of the layer of paint that coats the sharp edges of the metal split, the surface cannot avoid becomes duller. NeroForce has already improved this problem with the introduction of its Chrome Carbides. Instead of paint, a special metal layer is applied that is approximately 50 per cent thinner, which makes the tools much sharper. The new Densolit Carbides go one step further: the bionic sealing layer is approximately 75 per cent finer in comparison and is said to make the carbides sharper than all conventional tools, without compromising on rust protection.
Furthermore, the sharpness of the buffing tools is not affected by the fine protective layer and remains longer rough and aggressive. As the proportion of foreign material is minimal, the areas to be processed will be considerably less contaminated or not contaminated at all. At the same time, the heat generated by friction is reduced and the tools remain cooler for longer, which prevents the rubber in the working area from smearing. And there are two more benefits: service life increases “significantly”; and the Densolit surface treatment is purportedly “much more environmentally friendly than galvanic treatments or classic paint application”.
As a result of the treatment, Densolit Carbides are largely resistant to bending and abrasion, are temperature resistant and protected against corrosion. The combination of low temperatures and high abrasive power creates a high level of wear protection and leads to longer tool life.
According to the company, extensive tests have shown that NeroForce Densolit buffing tools can be used in a much more controlled manner and that buffing rubber is very efficient even without a lot of contact pressure. The tools remain precisely in the working area when working on surfaces without “wandering”.
“We will remain true to our philosophy of always questioning existing processes in order to find and develop more innovative solutions. Retreaders will be extremely satisfied with these new tools, because you can feel the difference immediately when working with them. Above all, extensive test series confirm that the innovative coating allows our customers to use the tools longer,” confirmed Andreas Müller, managing director of NeroForce.
“X-technology” for unit wheels
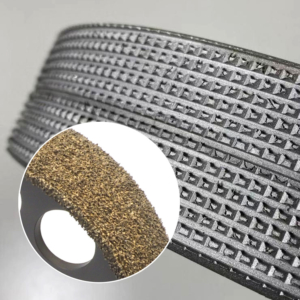
Such is the company’s confidence in this approach, soon NeroForce will gradually equip all conventional Unit wheels with the “X-technology” (Photo: NeroForce)
The second NeroForce introduction revolves around “X-technology” for unit wheels. Unit wheels are very popular for grinding tyre sidewalls, edges or conveyor belts. According to the company, the unique new “X-technology” from NeroForce ensures better removal of rubber dust from the working area, and more effective cooling without the need for cooling holes.
Unit wheels, which are nothing but Contour wheels with a flat profile, tend to contaminate the working area with rubber dust during grinding. NeroForce has now developed a simple solution to this problem: The surface of the base body consists of rows of trapezoidal recesses. Embossed grooves run between them, which not only removes the rubber dust from the working area due to the rotation of the grinding wheel, but also creates an air flow channel that significantly reduces the rising temperatures of the tool during grinding. This effect means that neither the tool nor the rubber heats up and the surface has a visibly more even texture. In addition, the adhesion of the Tungsten Carbide abrasive to the straight surfaces of the trapezoid is much better than is possible with a rounded profile. Extensive practical tests have shown that this technological concept significantly increases the service life of the new tools. Such is the company’s confidence in this approach, soon NeroForce will gradually equip all conventional Unit wheels with the “X-technology”, something company representatives say will noticeably improve the effectiveness of their tools.
Andreas Müller, founder of NeroForce, promises to concentrate the company’s focus on ground-breaking improvements of conventional tools in the future: “We see great potential in questioning the design and efficiency of conventional tools for rubber processing in order to significantly improve the effectiveness and results of these tools with innovative ideas”.
Comments