Continental’s Taraxagum project gains momentum
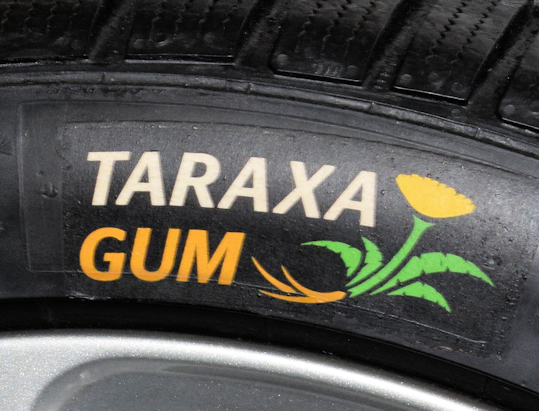
The miniscule pieces of plant root that Dr Tobias Ruckert shows us look for all the world like fresh spices, but the recipes he prepares with them aren’t for eating. Dr Ruckert is in charge of the R&D Mixing Laboratory at Continental’s Stöcken plant in Germany, and in this capacity is responsible for cooking up new and improved tyre compounds. The lab produces and tests more than 10,000 compounds a year, mostly to check materials or evolve existing compounds. But every so often Ruckert and his team have the chance to work with something new, with substances that offer an alternative to conventionally-sourced materials. This was the case when first handed the aforementioned plant roots early last decade.
These roots are from the Taraxacum kok-saghyz (TKS) plant, better known as Russian dandelion. Continental has been evaluating its suitability as an alternative source of natural rubber for much of the past decade. The team working on the project is small, but the results achieved so far impressive nonetheless. It was within Dr Ruckert’s lab in Stöcken, on the outskirts of Hannover, that we met two key team members to find out more about rubber from Russian dandelions.
Project leader Dr Carla Recker recalls the day in 2007 when Russian dandelions entered her world. “Representatives from two organisations, the University of Münster and Fraunhofer Institute for Molecular Biology and Applied Ecology (IME), gave me a tiny piece of brown, sticky rubber the size of a piece of chewing gum. They asked whether it’d be possible to make tyres from this material. That was the very beginning.” Dr Recker spent almost five years from that first encounter searching for the right partners for a joint project and securing the necessary funding; she’s now been involved in what’s known as the Taraxagum project for more than half her 24 years at Continental.
TKS – the wonder weed
With Taraxagum, Continental hopes for a source of natural rubber to complement the Pará rubber tree, Hevea brasiliensis. Dr Katharina Herzog, who’s worked on the Taraxagum project with Dr Recker as principal material developer since 2016, points out why a complementary source of natural rubber is so interesting: Global demand for the commodity is expected to grow two to three per cent annually, and a time will eventually come when from Hevea brasiliensis (Hevea rubber) supplies won’t suffice. “Demand will exceed supply sooner or later, therefore we need a second source.” Preferably a second source that doesn’t have to be shipped halfway around the world and isn’t affected by diseases that threaten Hevea rubber supplies; more on this later.
This relative of the weed found in many gardens is native to Kazakhstan, but Russian dandelion has the potential to grow in temperate climates from 30 degrees latitude – the region where Continental’s tyre factories in Europe and North America are located. It can be distinguished from the common dandelion by its smaller leaves, but the most interesting difference lurks underground: Russian dandelion roots contain a high proportion of rubber, between three and ten per cent of its dry weight. In comparison, the root of the common dandelion contains less than one per cent. The polymer that makes up around 95 per cent of this rubber is Cis-1,4 polyisoprene, identical to the polymer found in Hevea rubber.
‘Magic tonne per hectare’ key to viability
Continental is by no means the first to look at Russian dandelions as a potential source of natural rubber. Dr Recker relates that researchers in Russia sought an alternative to Hevea rubber early last century, culminating in large-scale efforts in the 1940s and early 1950s. “They produced tyres from dandelion rubber and these worked, but the project failed from an economic point of view,” she explains. Researchers were unable to achieve the required yield and they lacked a cost-effective means of extracting the rubber. Parallel attempts to produce rubber from Russian dandelions in Germany and the UK in the 1940s also petered out for similar reasons and increasing availability of synthetic rubber alternatives smothered further interest for half a century.
“We’ve proven that dandelion rubber is the equivalent of Hevea rubber in tyres, and we believe it can now be economically viable to produce, too,” states Dr Recker. Russian dandelion becomes viable as an alternative when a yield of one tonne to one and a half tonnes per hectare is reached, the same average yield gained from Hevea rubber. Dr Herzog speaks of the “magic tonne per hectare” as the main factor determining cost and commercial viability.
Farming dandelions in Germany
Ensuring sufficient yield has been central to the Taraxagum project since Continental began its partnership with the Fraunhofer IME, German federal research centre the Julius Kühn-Institute and Bavaria-based plant breeding specialist ESKUSA in 2012. The partners aim to cultivate a high-yield, undemanding strain of Russian dandelion. Dr Herzog mentions a challenge here: Russian dandelion is a very robust plant – when growing in the mountains of Kazakhstan. “It isn’t robust or invasive here in Germany. Other crops grow faster and suppress its growth. You have to take care, treat the plants like babies.”
The breeding programme to develop a more robust plant is still ongoing. New strains bred during the programme are evaluated in the northeast corner of Germany, where Continental has set up its Taraxagum Lab Anklam. This facility opened in December 2018 and utilises Russian dandelions grown by partner farmers in the Anklam region.
Travelling to Anklam from Continental’s home town of Hannover, where Carla Recker and Katharina Herzog are based, involves a drive or train ride of at least four hours. Such an out of the way location may seem an unusual choice, but Dr Recker explains that dandelions thrive in the region’s sandy soils. Furthermore, local farmers traditionally work with just a few crops and welcome the opportunity to rotate an additional alternative on their fields. Other factors, including support from the region’s government, played a role when choosing a site for the lab.
As of 2019, around 40 hectares of farmland in the Anklam region were dedicated to Russian dandelions, and the area will increase in future. It takes time to grow from small beginnings; dandelion is a completely new crop. “We’re learning how to grow this at the same time as the farmers are – learning by doing. Cultivating the crop on a large scale is completely different to growing plants in your garden,” comments Dr Herzog. To aid the partner farmers, the ten-person team at the Taraxagum Lab Anklam includes a farming coordinator.
Test tyres & commercial launch
Continental unveiled the first test tyres made using Taraxagum rubber in 2014. Dr Ruckert and his team were tasked with processing roots from Russian dandelion plants into suitable compounds. He met with “some surprises” when scaling the process up to the quantity required, but in the end produced a successful compound for a Taraxagum-based Continental WinterContact TS 850 P winter car tyre.
“Nobody believed we’d actually be able to build a tyre until that first example came out of the mould,” recalls Dr Recker. “We tested the tyres in every application, including handling, wet braking and rolling resistance. The results were positive, we discovered that Taraxagum really is an alternative natural rubber.”
The higher natural rubber content of winter tyres made them a logical choice for initial testing; the desired performance characteristics can be obtained without blending the compound. But Russian dandelion rubber is suited to all applications. Continental has tested it in various car tyres, truck tyres and other rubber products such as engine mounts. “The rubber worked well everywhere we applied it,” states Dr Recker.
They also tested it in bicycle tyres, and this product was chosen for Taraxagum’s commercial debut. The comparatively small amount of natural rubber required to make a bicycle tyre – typically less than 100 grams compared with one to three kilogrammes for a car tyre and up to 25 kilogrammes for a truck tyre – made it a good starting point for the fledgling Dandelion rubber programme. The Urban Taraxagum bicycle tyre came to market last year and celebrates its unorthodox material content with a tread pattern that resembles the structure of a plant cell as well as a dandelion seed design on the tread and shoulder area.
“There’s been much interest from cyclists and positive feedback from dealers,” comments Dr Recker. “The Urban Taraxagum ties in nicely with our Tour de France sponsorship.”
Industrialisation in 5 years
We’ll have to wait a little longer to see Taraxagum tyres for other vehicle types. Industrialisation of the rubber extraction process isn’t scheduled to begin for another five years, but once this milestone is reached Continental will bring Taraxagum into its tyre production straight away.
The priority in the meantime is to continue work on the breeding programme as well as research into an economic and ecologically sound extraction process. According to Dr Herzog, the company plans to invest 35 million euros in the Taraxagum project between 2017 and 2022.
Taraxagum to meet 10% of demand
Russian dandelion’s benefit to the tyre industry goes beyond its ability to meet growing demand for natural rubber. Shipping Hevea rubber from Asia to Northern Europe involves a sea voyage of 10,000 or more miles; dandelion rubber, on the other hand, could theoretically grow in fields adjacent to or down the road from Continental’s tyre making facilities in Europe. And as the plants reach maturity within a single season, everyone in the supply chain can respond to anticipated demand much more swiftly. Hevea brasiliensis requires seven years to mature, and trees are typically cut down at 25 to 30 years of age.
A further reason to champion natural rubber alternatives such as Russian dandelion becomes clearer when looking back over the rubber industry’s history. Brazil, home to the rainforest-dwelling Hevea brasiliensis, supplied around 99 per cent of the world’s rubber in the 19th Century. The figure today is less than one per cent, and the culprit behind this astounding drop is a fungus called Microcyclus ulei, which attacks the leaves of rubber trees and seriously affects latex production. Some fear that the fungus may spread to plantations in Asia one day.
“Therefore, it’s better to have another crop that offers an alternative. We want to become less dependent upon Asia and believe we can achieve with Russian dandelion the same annual yield per hectare as a rubber plantation,” stresses Dr Recker. She shares that with an equivalent annual yield, Russian dandelions could supply the entire current global demand for natural rubber with an area covering all of Austria and Switzerland under tillage – this is around 48,300 square miles, or just over half the United Kingdom’s land area. Continental isn’t aiming for this level of coverage, but its aims with Taraxagum are nonetheless ambitious.
“In seven to ten years we want to serve ten per cent of Continental’s global demand for natural rubber with Taraxagum. We think we can manage this,” states Recker. And as the company has no intention of taking coals to Newcastle – Katharina Herzog confirms that Continental is not planning to ship Taraxagum to Asia – European production sites will thus use more than the stated ten per cent.
“Farmers thought we were a bit crazy when we first said we wanted them to grow dandelions,” adds Dr Herzog. “But I believe they’ll have advantages with this crop in future. Farmers’ incomes in Germany are higher than those for rubber plantation workers in Asia, but they don’t have to go out every night to tap trees.”
Establishing a value chain
Taraxagum is on its way, yet the project is still a work in progress. The team is striving towards 100 per cent equivalency with Hevea rubber and will continue working towards this goal even after the process’s industrialisation mid-decade. Continental’s strategy regarding Taraxagum still hasn’t been finalised, either. Dr Recker outlines Continental’s main options: “We could market specific Taraxagum tyre lines, or we could use the rubber in all tyres made by a specific plant close to the Taraxagum facility. We haven’t decided yet.”
Nor has Continental decided upon certain aspects of Taraxagum production, including whether to work with a large, central facility or with smaller extraction operations adjacent to tyre plants. “Trials in Anklam will help us decide this,” comments Dr Herzog.
The question of value chain ownership also needs to be addressed. As Dr Recker notes, Continental’s traditional role has been that of a natural rubber consumer. “I don’t think we’ll turn into a dandelion farming company. We’re now helping to establish a Russian dandelion value chain in Europe. This will probably be independent, with us as a customer, but perhaps we’ll backwards integrate and own the processing plant.” The head of Materials Chemistry and Taraxagum admits that she doesn’t know which way Continental will decide.
Other consortiums around the world are also evaluating Russian dandelion rubber value chains – the Netherlands-based Drive4EU project and China’s Dandelion Rubber Industrial Technology Innovation Strategic Alliance are but two. Continental will by no means be alone in the sector in years to come. “Sooner or later, perhaps in 30 years’ time, I anticipate that Russian dandelion rubber will be a normal commodity that’s available for everybody,” predicts Dr Recker. “It will be a normal value chain that’s established around the globe. I’ll be happy if we’re still recognised as the ones who strove to do this first.”
Complementing, not replacing Hevea
While Taraxagum offers an antidote to fickle Hevea rubber prices and a future supply-demand imbalance, Carla Recker and Katharina Herzog stress again that Taraxagum is in no way intended to replace Hevea rubber. “Journalists from Southeast Asia sometimes ask us why we’re replacing natural rubber. We’re not – we want to serve additional demand. We don’t want to exchange production in Asia for Taraxagum.”
As mentioned, Hevea brasiliensis plantations will remain Continental’s sole source of natural rubber for production sites in Asia, and the company supports the Hevea supply chain through projects such as its Rubberway joint venture with Michelin and, in Indonesia, its partnership with the German Corporation for International Cooperation (GIZ).
I’m very proud of Continental
More than a dozen years have passed since that fateful encounter with a tiny piece of Russian dandelion rubber, but Carla Recker’s enthusiasm for the substance and its potential hasn’t waned. It’s still early days for Taraxagum. She sees its horizon stretching beyond 20 years and points out that a project of this length is unusual for a stock exchange listed company; results are typically demanded within three to five years. “The company is investing money even though it has to wait years before it sees the first big step,” she comments. “I am very proud of Continental for that.”
- s rubber obtained from the roots of Russian dandelions& Dr Carla Recker show u(l-r): Dr Katharina Herzog, Dr Tobias Ruckert
- Russian dandelion rubber (bottom left & in jar) is tested alongside other rubber varieties at Continental’s R&D Mixing Laboratory
- Since initially testing Taraxagum in a WinterContact TS 850 P car tyre, Continental has successfully evaluated it in a range of products
- The Urban Taraxagum bicycle tyre is the first commercially-available product made from the rubber
Comments