Borbet ramps up production at plant in Saxony, plans new facility
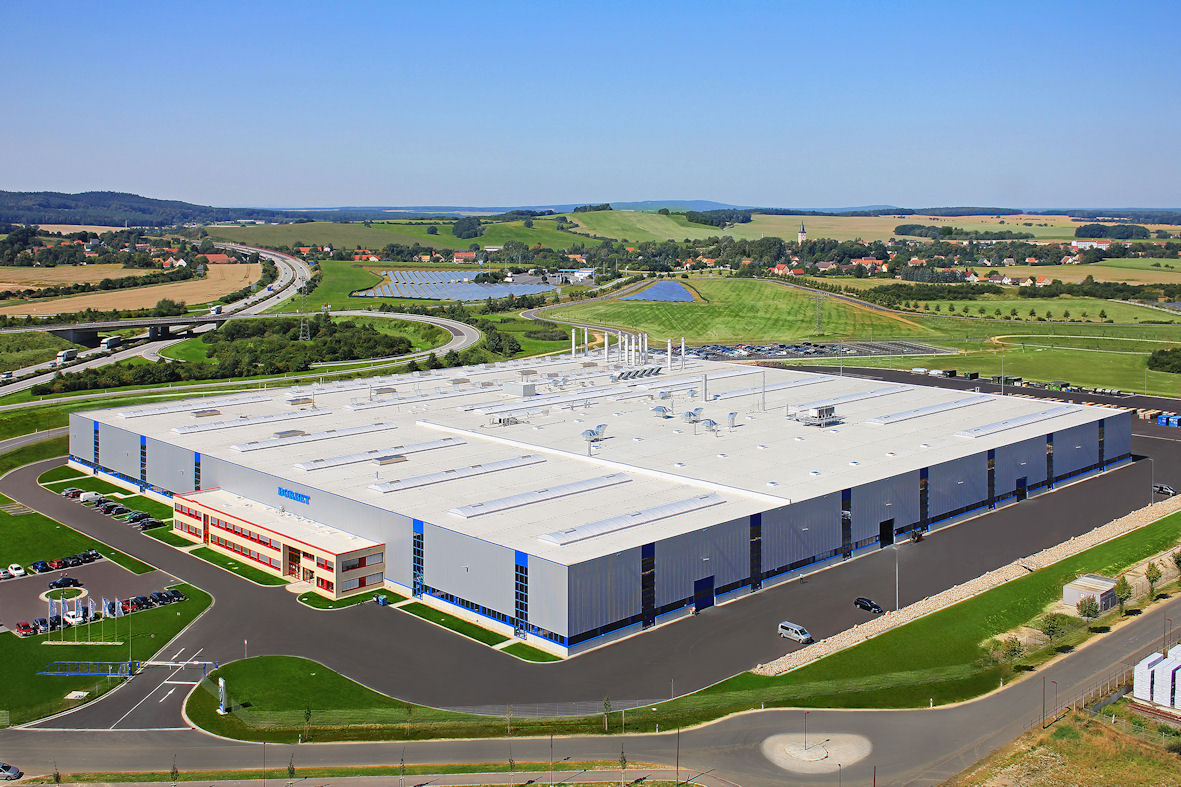
The new Borbet factory in Saxony, Germany is visible from afar – hardly surprising when bearing in mind that the plant’s floorspace sprawls over five entire hectares. The factory is located on a 12.3-hectare site near Görlitz, around four miles from the Polish border, and there is a good reason for building big: Saxony is an automotive stronghold, home to several major German vehicle manufacturers.
Company boss Peter Wilhelm Borbet travels from Borbet’s headquarters in North Rhine-Westphalia to the Kodersdorf plant in Saxony every two months together with his wife Margot and several employees, and the time he spends there is well-used. Peter Wilhelm Borbet engages in confidential discussions with key personnel such as plant manager Reiner Dürkop, and he takes a keen interest in new developments within the facility and listens to any issues his employees encounter or ideas they come up with. He identifies potential for further improvement in all areas – including the workforce. Approximately 420 people work at the plant at present, including 375 production and 45 administrative employees, with 18 per cent of the workforce coming from neighbouring Poland. When the plant reaches full production in the near future the employee headcount will exceed 450.
Workers trained in other Borbet plants
When full production capacity is reached in Kodersdorf in the near future, the plant will have a 450-strong workforce
Of course, not all production workers at the Kodersdorf facility are founders by trade. This isn’t necessarily an issue, as prior to starting work the employees receive training at the company’s other five plants in Germany. For example, 70 were “apprenticed” in production and in purchasing, quality control and administration at the Borbet facility in Bad Langensalza, Thuringia. The new recruits were licked into shape over a six-week period. In addition to communicating company-specific knowledge, the time spent there delivered an additional benefit. “If you know someone in the same position you can quickly call them should any questions arise,” comments Reiner Dürkop. The plant manager considers the training and further education of his workforce a priority, and from summer 2017 foundry mechanics will also be trained in Kodersdorf. Peter Wilhelm Borbet knows to appreciate his workforce’s performance: “Without them I’d never have been able to continually extend our company’s market share.”
Annual output to reach 2.5 million wheels
Alloy wheels are currently manufactured under a four shift-system. Should production rise in the coming months, it will run around the clock in a five-shift system. Production is at present focused upon 32 various wheel types from the more company’s comprehensive product portfolio, which includes more than 5,000 wheel specifications in total. Plant output is rising day-by-day. While half a million wheels were made between the plant’s completion in summer 2016 and the end of the year, the goal for 2017 is – depending on product mix – 1.6 million to 2 million wheels. By the end of next year around 2.5 million wheels should be shipped around the world from Kodersdorf annually. Between 80 and 90 tonnes of aluminium is prepared daily in five melting and five swarf furnaces for use in the plant’s 32 low-pressure die casting machines. The cast rims are x-rayed prior to entering the heat treatment facility. “Inspection is the be-all and end-all when it comes to manufacturing alloy wheels,” comments Dürkop.
Some 4,600 employees produce 20 million wheels a year in Borbet’s six German plants and in three further facilities in Austria, South Africa and the USA. Original equipment supply accounts for 97 per cent of these wheels, with the remaining three per cent sold by specialist retailers. Despite current turmoil within the automotive industry, Peter Wilhelm Borbet looks to the future with absolute confidence. A further factory is already being planned. While refraining from disclosing the exact location selected for this project, the company boss expresses a wish to expand Borbet’s production footprint in Germany. This wish is based on more than just strong local ties – he says the ‘made in Germany’ label counts as a “genuine competitive advantage.” christine.schoenfeld@reifenpresse.de/sg
Comments