Bridgestone tweaking kerb, tyre design for barrier-free bus travel
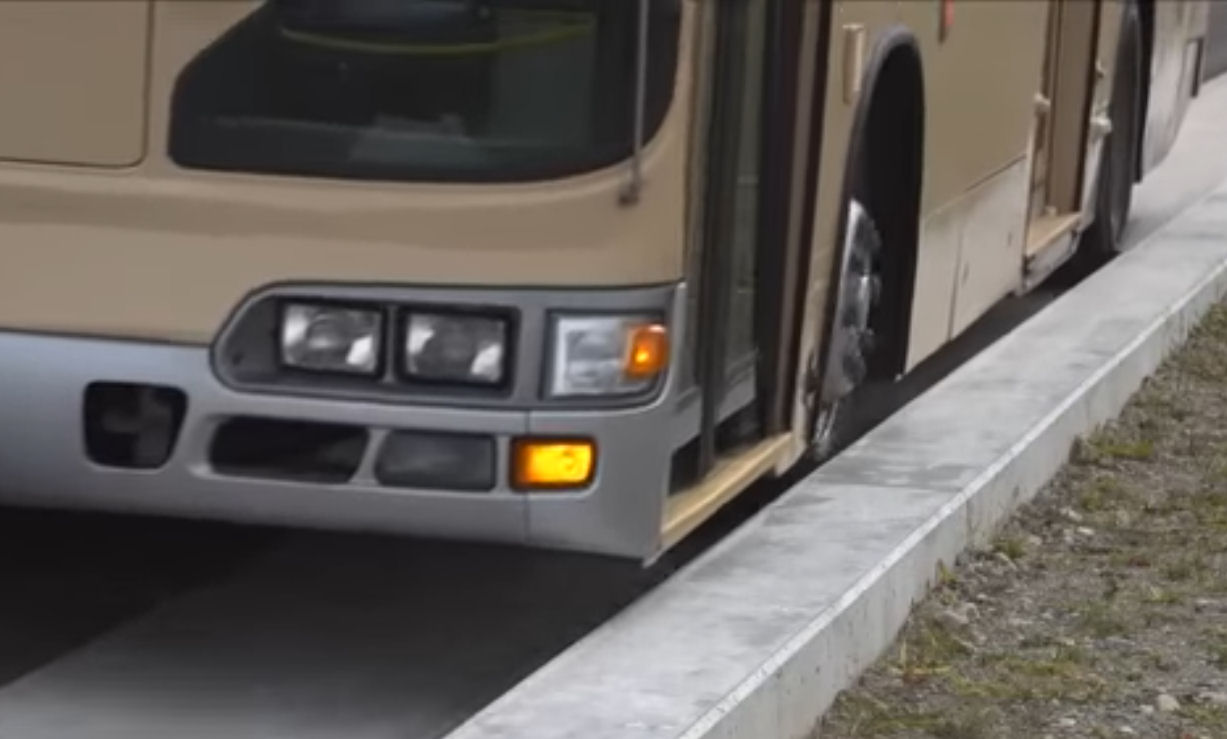
For over a year, Bridgestone Corporation has worked with partners to develop solutions that both facilitate barrier-free public transportation and protect tyres from sidewall abrasions. The company has reported on its progress towards achieving these goals and shared details of technologies that bring buses closer to the kerbside and also reduce tyre damage and discomfort to passengers should close turn out to be too close.
The first aim is to minimise the gap between the bus stop and the bus, an important consideration for physically-challenged individuals when boarding. Bridgestone has been working on a means of achieving this with Yokohama National University (Professor Fumihiko Nakamura of the Transportation and Urban Engineering Lab) since October 2015, and the Japan Transportation Planning Association joined the project in August 2016. The solution the partners have developed is low-tech but effective.
Bridgestone recently unveiled the partners’ idea for a sloping road edge that enables buses to approach the kerb naturally with minimal steering wheel manipulation. The company explains that “the road edge slope serves as a means of controlling the angle of approach to the kerb that isn’t dependent on the driver’s skill level,” and a video demonstrating this manoeuvre offers hope for every driver unburdened by talent for parallel parking. The kerb developed by Bridgestone and its partners features a ‘quarter pipe’ shape that reduces the shock experienced by a bus’s tyres and the bus itself when it comes into contact with the kerb.
Various sensors were employed during the concept’s development to measure vehicle behaviour and determine the dominant factors affecting kerb docking. Bridgestone also came up with a new method of simulating how a bus approaches a bus stop to help find the ideal kerb shape. Prototype kerbs were laid at Bridgestone’s proving ground in Nasushiobara City, Japan and testing carried out with urban buses. These tests showed that the average gap between the bus and the “next-generation docking kerb” was half that seen when stopping alongside a standard European kerb. The set target gap of less than 40mm was reached.
Tyre-based solutions
A better kerb design can help buses to stop closer to the footpath, but it can’t prevent drivers from striking the kerb entirely. This brings us to the second focus of Bridgestone’s public transportation project. The company is developing a wear-resistant technology for reducing tyre sidewall damage from contact with the kerb.
The technology is based on the concept of reducing the abrasive energy generated from contact between the tyre and the kerb. Bridgestone is keeping its cards close to its chest and has only described its solution in loose terms, however the company confirms that the benefits of its wear-resistant technology have been confirmed through tests of prototypes. Based on quantitative data about kerb contact collected through tests and simulations, Bridgestone anticipates the material it has developed will help reduce tyre sidewall wear by approximately 30 per cent.
Comments