Twaron and aramid
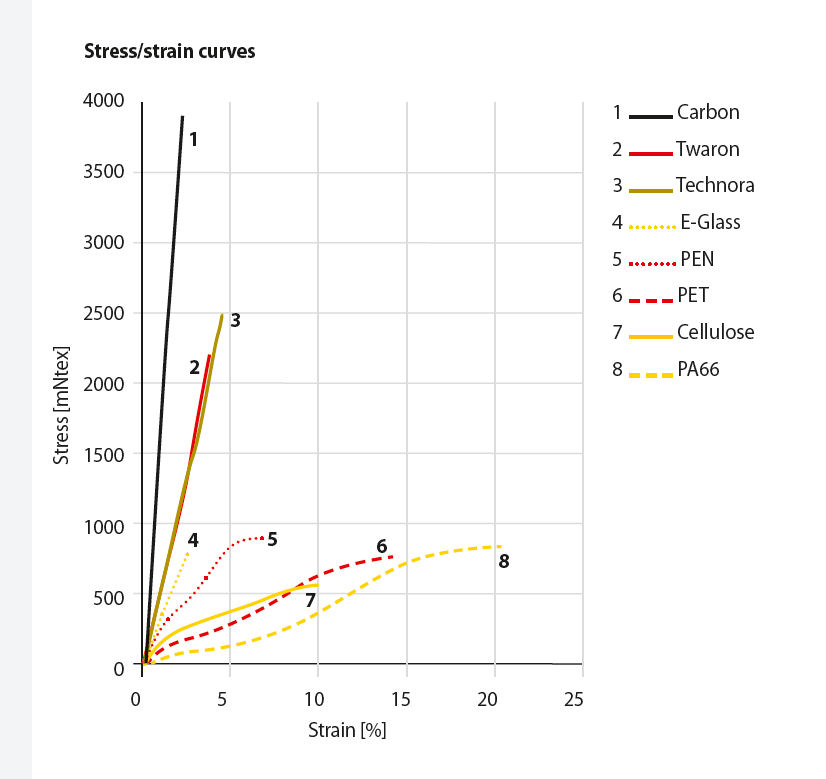
Twaron is produced from a para-aramid that Teijin Aramid makes itself in facilities in Delfzijl and Emmen, the Netherlands using raw materials sourced from the oil industry. As explains Dr. Ir. Bert Gebben, group head of Wet Spinning within the R&D facility at the company’s headquarters in Arnhem, the para-aramid is formed through the reaction between an amine group and a carboxylic acid halide group. The resulting polymer has a rigid, rod-like structure, unlike the ‘cooked spaghetti’ structure of most plastics, and Gebben observes that the structure and qualities of the para-aramid make the job of converting it into a usable product a very complicated one.
“Most synthetic yarns are made by melting, you just increase the temperature of the polymer and it becomes a liquid, but aramid cannot melt so must be made into a solution with a solvent,” Gebben explains. “The long rigid rods are very difficult to dissolve, and the only available solvent is 100 per cent concentrated sulphuric acid. The resulting dissolved solution has the appearance of a solid, and thus it must be heated to more or less melt it into a very viscous solution that hardly flows at room temperature. The solution is pressed through a spinning plate (which, to continue the spaghetti metaphor, looks like a colander) covered with hundreds of small holes. The filaments are joined together to make a yarn, with each yarn containing 1,000 filaments.
“The filaments are not glued to each other – they are all effectively separate, but are bundled into one yarn. To solidify the yarn it then goes into water baths to wash the sulphuric acid out before it is dried wound onto a bobbin,” Gebben adds. “This is our basic product, it is used with slight adaptions in tyres and other applications. But it must be made into a cord for use in tyres.”
Much of Gebben’s work is carried out at a pilot Twaron pilot line set up in Arnhem some 40 years ago and dedicated to research and development purposes. The pilot line and associated R&D facility is also home territory for Ing. Michel van den Tweel, who is responsible for product evaluation and adhesion at the centre’s Technical Fiber Applications department. Van den Tweel’s job involves, amongst other things, exploring the potential of aramid and aramid blends in specific applications. He shares that the performance of a fibre can be altered or influenced in three main ways – through the choice of aramid, the material the aramid is paired with and how the two are twisted together, and the conditions under which the resultant cord is dipped.
“We have different aramid types for all applications,” explains van den Tweel. “Our material portfolio includes standard, high elongation, high tenacity, high modulus and high strength materials. But that’s not the end of the story, as when you twist the material you can utilise combinations. You can combine one aramid with another or – and this is very important for the tyre industry – you can create hybrid constructions. When we talk about hybrid constructions we mean the pairing of a very strong aramid with a low modulus polyamide or a polyester. I call this ability to experiment with a vast range of combinations the ‘playground’ as it gives us a complete portfolio of tensile curves for what we require or desire, and our findings are often very interesting for the tyre industry.”
As pure aramid does not elongate, it can be necessary to mix it with polyamide for use in, for example, a tyre’s cap-ply. “A green tyre expands when forming the tread surface print in the mould, this tyre lift is approximately two to four per cent,” comments van den Tweel. “Pure aramid could simply cut through the rubber.”
After the selected aramid is paired and twisted with a polyamide or polyester, it is ready for dipping. “Here at the R&D centre we use a typical three-oven dipping system,” shares van den Tweel. “In the oven you have the three ‘T’s – time, temperature and tension – and all three are important for a material’s final properties.” Dipping improves thermal stability and consolidates the filament bundle, and van den Tweel notes that while aramid is more or less indifferent to the dipping process, it can strongly influence the polyester or the polyamide. “Dipping is just as important as twisting as far as tuning a material to the customer’s requirements goes.”
In addition to its use in casing cord, dipped Twaron fibre can also chopped into small lengths (typically between 1mm and 6mm) and mixed into rubber compound in order to reinforce the stiffness of the rubber. Some manufacturers add these chopped Twaron fibres to sidewall compound. “If you want to have a sidewall with a higher modulus, you can use this kind of material,” comments Sjaak Bensink. “In some cases it is also being used in run-flats and puncture-resistant tyres.”
Aramid short fibres can also be added to rubber compound in order to reduce its hysteretic properties, which translates into better rolling resistance and improved durability. Teijin Aramid markets such a product under the brand name Sulfron. When added to rubber compounds, Sulfron can improve several properties. These include an increase in the low strain modulus, abrasion, puncture and tear resistance, dynamic fatigue properties, energy loss and green strength. The loading required is typically much lower than for other short fibres minimising adverse effects, such as wicking and permeation. stephen.goodchild@tyrepress.com
Comments