Physical breaks designed to counteract fire risk
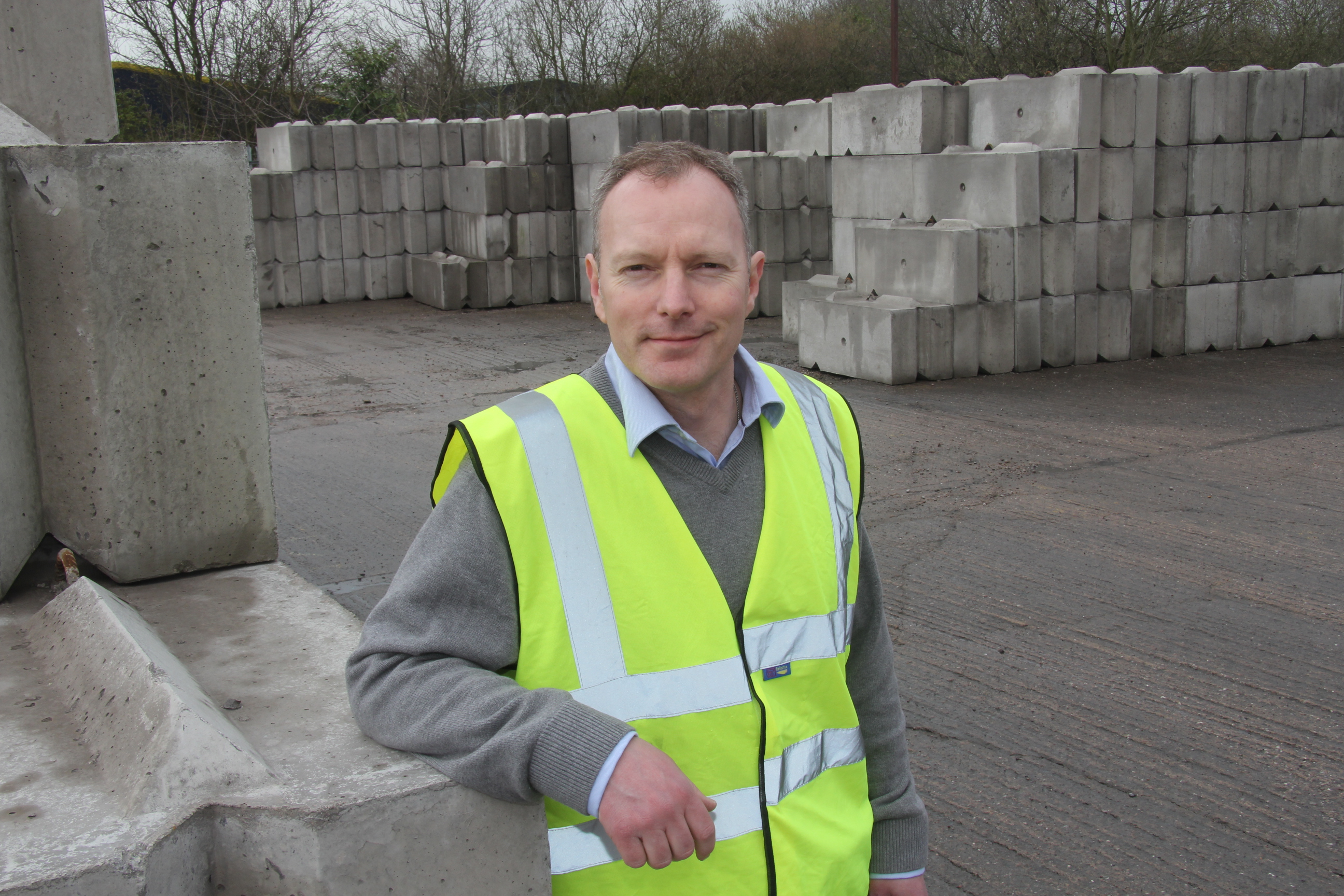
Why tyre recycling firms need more sophisticated disaster recovery plans
Fires at tyre recycling and processing sites have long been a problem. In order to offer a solution Owen Batham, sales and marketing director of Elite Precast Concrete Ltd, suggests there is a growing need for firms to take a more proactive approach to their fire risk management and to develop more sophisticated disaster recovery plans.
According to Elite, current legislation and best practice is based on Pollution Protection Guidance (PPG29) which recommends using a combination of maximum stack sizes and minimum separation distances between stacks of materials as the primary risk management strategy. Written as a regulatory guide for the safe storage of combustible materials to prevent and control fire, PPG29’s aim is to provide companies with appropriate standards and to share best practice for the management of fire risk involving storage facilities. Furthermore Elite reports, that its focus is almost exclusively on the use of specified gaps and distances between bays of stacked materials, and this one-size-fits-all approach is pretty much the only one offered by the guidelines, which fail to consider any alternative or additional approaches that could be used.
With the increasing placement of tyre plants and waste management, treatment, and storage sites in city centre and urban locations – where space is at a premium – adherence to PPG29 can be prohibitively expensive and not necessarily the most effective solution. “Rather than simply focusing on gaps between stockpiles, I believe that we should focus on the use of physical fire breaks as these not only make great sense from a health and safety perspective, but they’re a commercially-astute decision too,” Owen Batham explained.
The thinking is that free-standing, high-quality, physical fire breaks can both reduce the risk of fires spreading and allow businesses to make more efficient use of their sites by permitting larger material stacks, and using up space which otherwise would have had to be left clear. And by using freestanding interlocking concrete blocks to form these fire breaks, not only can the costs and inconvenience of permanent footings be avoided, but the bay walls and fire breaks themselves can be easily dismantled and reassembled by unskilled personnel, which allow facilities to keep up with changing recycling trends, storage needs, and business demands.
Concrete fire breaks are a hugely strong, readily available, and cost-effective solution, and concrete itself in no way contributes to the breakout or spreading of fires and – unlike steel or timber – concrete has the lowest rate of temperature rise across a surface, and through the cross-sections of concrete internal zones don’t reach the same high temperatures as a surface exposed to flames. Put simply, concrete does not add to a fire’s fuel load, and very few other, cost-effective materials can argue the same.
Quality precast interlocking concrete blocks also don’t omit any toxic gases or fumes, are resistant to smouldering materials, and – if properly designed and manufactured – can be described as ‘fire-proof’. To this end there are British and European Standards to distinguish whether concrete blocks are fit-for-purpose and these very much focus on the constituent ingredients of the concrete. Therefore Elite recommends you should only consider blocks which comprise of less than 1 per cent organic constituents and recycled materials and are therefore Class 1A Fire Resistant based on clause 4.3.4.4 of EN 13369.
“The time is absolutely right for new guidelines to be developed, but until then I urge tyre waste and recycling businesses to consider the use of physical fire breaks as part of their armoury in the war against fire. Speak with your local fire safety officer, liaise with your industry bodies, and speak with your colleagues, competitors and the wider industry. We need to work together to evolve outdated guidance into something ready not only for 2014 but for the years to come” concluded Owen.
Founded in 2008 by a team with more than 40 years industry experience, Shropshire-based Elite Precast Concrete Limited is the UK market leader in manufacturing and supplying Duo interlocking, Vee interlocking and Legato interlocking precast concrete blocks. The company’s precast concrete products are now used by a wide range of national and international clients including local authorities, tyre plants, recycling businesses, and waste management firms, to build durable waste storage bays.
Comments